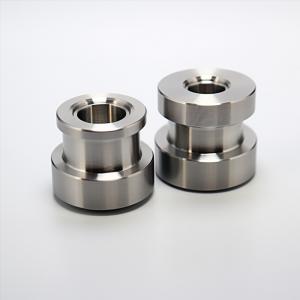

Add to Cart
CNC machining represents the predominant subtractive manufacturing technology in
contemporary industrial processes. It stands as an exceptionally flexible and robust method
for the production of tailor-made metal and plastic parts.
Leveraging CAD models, CNC machines execute precise material removal from solid blocks
through a diverse range of cutting tools.
In essence, CNC machining yields components characterized by precise tolerances and
remarkable material properties. Its applicability spans from individual projects to low-to-medium
volume production runs (up to 1,000 parts), primarily due to its exceptional repeatability.
Nevertheless, it is important to acknowledge that CNC machining entails specific design
constraints, partly attributed to its subtractive nature, setting it apart from 3D printing.
Product Details
CNC milling encompasses a wide range of materials, with three main categories: plastics, soft
metals, and hard metals. These materials are versatile and suitable for various machining
applications.
Examples of materials used in CNC milling include aluminum, bronze, copper, ceramics, plywood,
various types of steel, stone, wood, and zinc, among others.
Certain materials, such as aluminum and mild steel, are favored by machinists due to their ease
of workability and excellent properties, making them industry standards for many applications.
Common Materials | |
Name | Description |
Aluminum | High machinability and ductility, good strength-to-weight ratio. |
Stainless steel | High tensile strength, corrosion and temperature resistant. |
Mild steel | High machinability and weldability, high stiffness. |
Brass | Low friction, excellent electrical conductivity, golden appearance. |
Copper | Excellent thermal and electrical conductivity. |
Titanium | Excellent strength to weight ratio, used in aerospace, automotive and medical industries. |
ABS | Common thermoplastic, impact resistant, easy to machine. |
Nylon | Excellent mechanical properties, thermal, chemical and abrasion resistant. |
PEEK | High-performance thermoplastic, very high strength, thermal and chemical resistant. |
Surface Finishes | ||
Name | Applicable to | Machining marks |
As machined | Metals, Plastics | Visible, light surface scratches |
Smooth machining | ||
Fine machining | Metals | Slightly visible |
Polishing | Metals | Removed on primary surfaces |
Bead blasting | Metals | Removed for non-cosmetic, removed on primary surfaces for cosmetic |
Brushing | Metals | |
Anodizing Type II | Aluminum | |
Anodizing Type III | Aluminum | Visible under anodizing |
Black oxide | Copper, Stainless steel, Alloy steel, Tool steel, Mild steel | Visible |
Powder coating | Metals | Removed |
Brushed + electropolishing | Stainless steel | Removed on Primary surfaces |
Specialist Industries
CNC machining is a go-to manufacturing process to get precision parts, whether for prototyping or
end-use production.
It is widely used throughout the aerospace, medical, automotive industries for its ability to rapidly
manufacture precise parts in production-grade materials, such as:
1. housings and enclosures
2. brackets
3. fixtures for manufacturing
4. gears and bearings
5. internal mechanical components
6. medical instrumentation
Company Profile
FAQ's
1. A quick guide to CNC machining parameters
Many of the crucial machining parameters are established by the machine operator during the
generation of G-code. Among the primary parameters we will discuss are the CNC machine's build
size and its precision.
CNC machines are equipped with a relatively spacious build area, particularly when compared to
3D printers. CNC milling systems are capable of machining parts with dimensions of up to
2,000 x 800 x 100 mm (78” x 32” x 40”), while CNC turning systems excel at machining parts
with diameters reaching up to Ø 500 mm (Ø 20’’).
CNC machining empowers the creation of components with exceptional accuracy and stringent
tolerances. These machines are capable of achieving tolerances even finer than half the diameter
of an average human hair, with a precision of ± 0.025 mm or .001’’.
In cases where tolerances are not explicitly specified in the technical drawings, operators typically
machine the part with an accuracy of 0.125 mm (.005’’).
2. How much do CNC machining materials cost?
The cost of materials in CNC machining can fluctuate significantly due to the extensive array of
available options. Each material carries its unique price tag, and the inherent physical properties
of each material play a substantial role in determining machining costs.
For those seeking to manufacture metal components, Aluminum 6061 stands out as the most
cost-effective choice. On the other hand, ABS ranks as the most budget-friendly option among
materials.
As for the influence of machining complexity on costs, stainless steel serves as an illustrative
example. Its inherent hardness, surpassing that of aluminum, renders it more challenging to
machine, consequently elevating the overall machining expenses.
3. What's the general surface texture of CNC milled and turned parts?
In the realm of CNC machining, as-machined milled parts typically exhibit a surface roughness
of approximately 3.2μm (or 1.6μm in the case of relatively new machines).
On the other hand, when it comes to turned parts, we can achieve a smoother surface with a
roughness of 0.8μm. This means that machining speed adjustments are not necessary to attain
this level of surface finish.