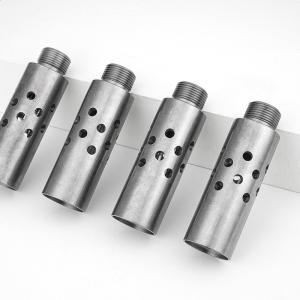

Add to Cart
CNC Machining Service Parts High Precision CNC Turning Stainless Steel Machining
Parts Milling Steel Parts
CNC, short for computer numerical control, defines a machining process driven by computer
commands. This technology enables faster, more accurate, and intricate part production compared
to manual methods.
CNC machining reduces reliance on manual labor while enhancing precision and complexity.
Although humans are vital for programming and machine operation, the physical machining tasks
are automated.
This synergy between human expertise and computer-driven automation ensures seamless and
efficient operations.
Product Details
CNC machines excel at cutting a wide range of materials, including aluminum, bronze, copper,
ceramics, plywood, various steel types, stone, wood, zinc, and numerous engineering materials.
This versatility makes them perfect for crafting prototypes during product development.
With CNC milling, you can easily fine-tune and make precise adjustments until you achieve the
desired final product, offering accuracy and efficiency throughout the manufacturing process.
Here is a comprehensive overview of the most popular materials
The Most Popular Materials | |
Material | Characteristics |
Aluminum 6061 | Good strength-to-weight ratio, excellent machinability, low hardness |
Stainless Steel 304 | Excellent mechanical properties, resistant to corrosion & acid, relatively difficult to machine |
Mild Steel | High machinability and weldability, high stiffness |
Brass C360 | High ductility, excellent machinability, good corrosion resistance |
Alloy Steel | High strength and toughness, fatigue resistant |
Copper | Excellent thermal and electrical conductivity |
Titanium | Excellent strength to weight ratio, used in aerospace, automotive and medical industries. |
ABS | Excellent impact resistance, good mechanical properties, susceptible to solvents |
Nylon (PA6 & PA66) | Excellent mechanical properties, high toughness, poor moisture resistance |
POM (Delrin) | High stiffness, excellent thermal & electrical properties, relatively brittle |
Surface Finishing
We specialize in the production of custom-made products and offer surface treatment services
tailored to meet our customers' specific requirements and industry standards.
Our comprehensive solutions are both efficient and cost-effective, making us a one-stop destination
with the capacity and capability to provide integrated services.
Surface Finishing Options for CNC Machining | ||
Name | Applicable Materials | Can be Applied with |
Alodine | Aluminum | Media Blasting, Tumbling, Type II Anodizing* Type III Anodizing*, Type III Anodizing with PTFE* |
Anodizing | Aluminum | Media Blasting, Tumbling, Alodine* |
Black Oxide | Steel, Stainless Steel | Media Blasting, Tumbling, Passivation |
Electroless Nickel Plating | Aluminum, Steel, Stainless Steel | Media Blasting, Tumbling |
Electropolishing | Steel, Stainless Steel | — |
Hand Polishing | Acrylic | Enhanced cosmetic appearance |
Media Blasting | Aluminum, Steel, Stainless Steel, Brass, Bronze, Copper | All post processes except Electropolish and Powdercoat |
Nickel Plating | Aluminum, Steel, Stainless Steel | Media Blasting, Tumbling |
Passivation | Steel, Stainless Steel | Black Oxide, Electroless Nickel Plating, Zinc Plating, Tumbling, Media Blasting |
Powder Coating | Aluminum, Steel, Stainless Steel | — |
Tumbling | Aluminum, Steel, Stainless Steel, Brass, Bronze, Copper | All post processes except Electropolish and Powdercoat |
Vapor Polishing | CNC Polycarbonate (Clear, Black) | Enhanced cosmetic appearance, near optically clear applications |
Zinc Plating | Steel, Stainless Steel | Media Blasting, Tumbling, Passivation |
Specialist Industries
CNC machining services find applications in various industries, catering to specific needs and
demands:
1. Transportation: CNC turning plays a vital role in crafting components for the aerospace,
automotive, mass transit, rail, locomotive, military, and trucking sectors.
These industries rely on CNC machines to produce essential parts like headnuts, gear blanks,
bearing blocks, levers, axles, and rotors for transportation equipment.
2. Construction: The construction industry requires robust components capable of withstanding
heavy loads.
CNC machining is frequently employed to manufacture bolts and screws from materials like
stainless steel and aluminum, essential for assembly and fastening tasks.
3. Automotive: CNC turning services are indispensable in the automotive sector, producing critical
auto parts including cylinder heads, connecting rods, camshafts, transmission components like
shafts and rings, suspension parts such as sway bars, control arms, tie rod ends, as well as various
items like bushings and bolts.
4. Aviation: The aviation industry heavily relies on CNC turned parts for customization and the
production of probes, joint connectors, fasteners, and engine and aircraft components.
Many aviation components utilize titanium due to its ability to withstand extreme temperature
variations, making it a preferred material for critical applications.
Company Profile
How to Reduce CNC Machining Costs?
To reduce CNC machining costs effectively, a comprehensive approach that optimizes various facets
of the manufacturing process is essential.
By implementing the following cost-saving strategies, manufacturers can enhance efficiency and
maximize their cost optimization efforts:
1. Supplier Collaboration: Collaborating with CNC machine suppliers is invaluable for exploring
cost-saving opportunities. Engage with suppliers to negotiate favorable pricing, especially for bulk
material purchases.
Solid supplier relationships can optimize supply chain logistics, improve delivery times, and reduce
transportation costs.
These collaborative efforts can also lead to innovative solutions and cost-saving recommendations
based on suppliers' expertise in the CNC machining industry.
2. Design Optimization: Designing parts with manufacturability in mind is crucial for CNC machining
cost reduction. Streamlining the machining process by simplifying geometry, minimizing tight
tolerances, and reducing the number of operations can minimize material waste and production time.
Collaborating with design engineers to optimize part designs for CNC machining significantly lowers
tooling requirements and overall costs.
3. Material Selection and Standardization: Careful material selection and standardization can yield
substantial cost savings.
Choosing cost-effective materials that meet specifications and standardizing material options across
product lines can simplify procurement, minimize waste, and enhance machining efficiency.
Factors such as material availability, price, and compatibility with machining processes should be
considered during material selection.
4. Process Optimization: Optimizing the machining process is essential for cost reduction.
This involves evaluating and refining various production aspects, including toolpath optimization,
setup time reduction, machine utilization improvement, and implementing lean manufacturing principles.
Optimizing toolpaths, reducing unnecessary movements, and minimizing setup time enhance productivity
and lower costs. Implementing lean manufacturing techniques like 5S, value stream mapping, and
continuous improvement initiatives further contribute to cost optimization.
5. Automation and Robotics: Integrating automation and robotics into CNC machining processes can
significantly enhance efficiency, reduce labor costs, and improve productivity.
Automated systems handle repetitive tasks, allowing skilled operators to focus on complex operations.
Robotics ensures precise and consistent machining, resulting in higher-quality parts and reduced scrap.
Embracing automation and robotics increases throughput, reduces labor expenses, and improves
process control, leading to substantial cost savings.
By implementing these cost-saving strategies, manufacturers can effectively reduce CNC machining expenses,
enhance their competitive edge, and maintain high-quality production.