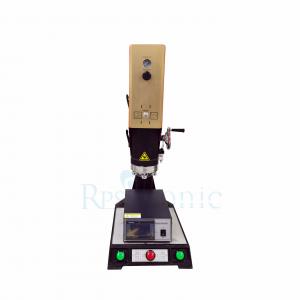

Add to Cart
Parameter
Frequency | Power | Working distance | Input voltage | Air pressure | System language |
15Khz | 2500W/3000W/4000W | 75mm/100mm | 220V or 110v | 0.2-0.8Mpa | English/Chinese |
20Khz | 2000W/3000W | 75mm | 220V or 110v | 0.2-0.8Mpa | English/Chinese |
30Khz | 1000W | 75mm | 220V or 110v | 0.2-0.8Mpa | English/Chinese |
35Khz | 1000W | 75mm | 220V or 110v | 0.2-0.8Mpa | English/Chinese |
40Khz | 800W | 75mm | 220V or 110v | 0.2-0.8Mpa | English/Chinese |
Description
Ultrasonic welding is a high-tech technology for welding thermoplastic products. All kinds of thermoplastic rubber parts can be processed by ultrasonic welding without adding solvents, adhesives or other auxiliary products. Its advantages are to increase productivity by multiple times, reduce costs, improve product quality and safe production.
The principle of ultrasonic plastic welding is that a generator
generates 20KHZ (or 15KHZ) high-voltage and high-frequency signals,
and converts the signals into high-frequency mechanical vibrations
through the energy conversion system. The signals are applied to
the plastic workpiece and pass through the surface of the workpiece
and internal molecular parts The friction causes the temperature of
the transfer to the interface to rise. When the temperature reaches
the melting point of the workpiece itself, the interface of the
workpiece melts quickly, and then fills the gap between the
interfaces. When the vibration stops, the workpiece is cooled and
set under a certain pressure at the same time. Welding is achieved.
When ultrasonic waves act on the thermoplastic plastic contact
surface, it will produce tens of thousands of high-frequency
vibrations per second. This kind of high-frequency vibration with a
certain amplitude will transmit the ultrasonic energy to the
welding area through the upper weldment. Because the welding area
is two The acoustic resistance at the interface of each welding is
large, so local high temperature will be generated. In addition,
due to the poor thermal conductivity of the plastic, it cannot be
distributed in time for a while, and it gathers in the welding
area, causing the contact surface of the two plastics to melt
rapidly, and after a certain pressure is applied, they are fused
into one. When the ultrasonic stops, let the pressure continue for
a few seconds to make it solidify and shape, thus forming a strong
molecular chain, achieving the purpose of welding, and the welding
strength can be close to the strength of the raw material. The
quality of ultrasonic plastic welding depends on three factors: the
amplitude of the transducer's welding head, the applied pressure
and the welding time. The welding time and welding head pressure
can be adjusted, and the amplitude is determined by the transducer
and the horn. There is an appropriate value for the interaction of
these three quantities. When the energy exceeds the appropriate
value, the melting amount of the plastic is large and the welded
material is easy to deform; if the energy is small, it is not easy
to weld firmly, and the applied pressure cannot be too large. This
pressure is the product of the side length of the welded part and
the pressure per 1 mm of the edge.
Features
Using microcomputer control system, the machine is stable and
reliable;
Frequency automatic compensation circuit
Piezoelectric ceramic transducer, strong and stable output
The whole machine adopts a motor electric lifting system, which is
convenient to adjust;
The welding head level adjustable structure is adopted, which is
convenient for mold adjustment;
Adopt square column and dovetail groove structure, so that the
position of the machine is not suitable to shift, and the
positioning is accurate
Pictures