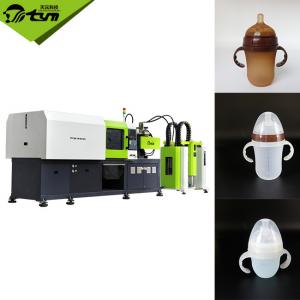

Add to Cart
Advantages of liquid silicone materials
1. High and low temperature resistance: the adaptive temperature
range of silica gel is -40~230 degrees, can be refrigerated (ice
cream mold), can be microwave (silica gel fresh bag, lunch box,
etc.).Flexibility: this is also a feature of the raw material
itself, the silicone products produced can be easily folded,
stretched, a second rebound, not easy to deformation.
3 easy to clean: this kind of product surface smooth, feel
comfortable, was not easy to stain, usually after using water rinse
can be clean.4 wear resistance: the mouse pad and the buttons of
the remote control are made of silica gel. It seems that they have
never been worn out. At most, the patterns on them can't be seen.5
long life: its chemical properties are stable, not burning, not
water absorption, not conductive, fully combined with the above
characteristics, can be concluded that the average service life of
silicone products are very long, 6 natural environmental
protection: silicon is a natural material in nature, non-toxic
harmless
Machine Model
Machine Model | Shot Volume | Injection Rate | Injection Pressure | Clamping Force | Opening Stroke | Tie-Bars Space | Ejection Force | Machine Weight | Motor Power |
TYM-L5058 | 165g | 30g/s | 700kg/cm2 | 130T | 250-550MM | 500*580MM | 4.3T | 5.3T | 12.1kw |
TYM-L6068 | 300g | 30g/s | 700kg/cm2 | 130T | 250-550MM | 600*680MM | 4.3T | 5.5T | 12.1kw |
TYM-W4545 | 165g | 30g/s | 700kg/cm2 | 130T | 200-700MM | 450*450MM | 4.3T | 5.2T | 12.1kw |
TYM-W5050 | 300g | 30g/s | 700kg/cm2 | 130T | 200-700MM | 500*500MM | 4.3T | 5.3T | 12.1kw |
The key points for LSR to achieve precision injection molding are
as follows:
(1) full mixing of liquid silica gel
➀ accurate mixture ratio: the LSR two-component materials A and B,
in front of the injection molding, must, in accordance with the
exact 1:1 mix, if it is colored liquid silicone products, also must
be precise control paste ratio.
➁ mixer, static mixer is the key parts of injection molding, A, B
glue only after static mixer mixing adequately, can ensure
completely vulcanization molding liquid silicone injected into the
mold.
(2) sealing and temperature control of injection molding machine
parts
➀ attributed to LSR low viscosity, the reverse flow of materials
and glue leakage, must to seal screw;
➀ because LSR molding process of mould is heated, in order to
prevent LSR curing, can adopt the structure of the water-cooled
nozzle to keep the temperature low enough.
(3) finished product control during injection molding
➀ parting line: consider the location of the parting line and
precision in advance, help to avoid air entrainment and welding, to
avoid flash;
➁ contraction: although LSR no shrinkage in injection molding, but
due to its high thermal expansion coefficient, usually after
stripping, cooling the contraction of 2% ~ 3%;
➂ injection gate location: need to consider the actual product
shrinkage;
➃ vacuum: when designing die line to ensure that the mold closed,
vacuum pump through mould switch the following fixture will all
cavity vacuum;
➄ demoulding: generally USES the fractionating column plate and
ejector pin and the air ejector demoulding technology, or a manual
release.
➅ mold temperature: LSR is in heating vulcanization molding, must
control the mold temperature is uniformly distributed.The
temperature difference is controlled at +/-10℃.