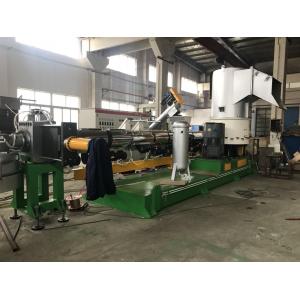

Add to Cart
Plastic Waste Recycling Granulator Machine For Film And Bags
LIANDA Design
Film compacting pelletizing system, it is a three in one recycling machine designed for low density plastic articles. It will provide the excellent re-pelletizing and recycling solution for film, raffia, filament, woven bag and nonwoven fabric and other consumed / post soft or rigid plastic. Our pellet making machine has a wide application in PE, PP, CPP, BOPP, PS, PPS, EPS, ABS, PA, PLA, PET waste plastic materials recycling field.
No | Machine Name | Quatity (set) |
1 | Belt conveyor | 1 |
2 | Film compactor/Agglomerator | 1 |
3 | Single Screw Extruder (Single or Double step ) | 1 |
4 | Vacuum degassing system | 1 |
5 | Hydraulic screen changer filteration system | 1 |
6 | Water-ring pelletizing system | 1 |
7 | Dewatering machine | 1 |
8 | Vibrating sieve | 1 |
9 | Air conveying system | 1 |
10 | Control system | 1 |
Model | Screw diameter First step (mm) | Screw diameter Second step (mm) | Main motor kw | Second motor kw | Output Kg/h |
85/100 | 85 | 100 | 45/55 | 22 | 200 |
100/120 | 100 | 120 | 75/90 | 37 | 350 |
130/140 | 130 | 140 | 132 | 45 | 600 |
160/180 | 160 | 180 | 185 | 55 | 850 |
180/200 | 180 | 200 | 220-335 | 75 | 1200 |
3.Working processing
1.The plastic material feed through belt conveyor get into the compactor.
2.Film compactor/Agglomerator will cut film and compact the film by friction
●The rotatory blades of compactor will cut up incoming scraps.
3.The compacted film will be fed to Extruder by special design drop guide
4.The screw extruder will have the processing of Plastified while the material fed to the extruder. And the vacuum degassing system will remove the water moisture of the material and clearance of low molecular to improve the quality of finished pellets
●A specialized single screw extruder applied to gently melt the pre-compacted material.
A screen changer can be installed before die head to remove some metal, wood, dust, paper such impurities to get high quality output plastic melt.
Controlling System
Advantage of he machine line
Advantages | |
1 | Automatic design Siemens PLC control system |
2 | The Film compaction/ agglomerator is designed with observation window to facilitate customers to open,clean and change the blades |
3 | The speed of the cutting motor of the compaction cylinder is adjustable to realize the closed-loop control of the speed of the extruder |
4 | The specially designed valve structure on the entrance of screw extruder, which effectively controls the moisture of the material entering the extruder, ensuring the stability of the discharge and the quality of the raw material |
5 | Realize the continuous production of film transportation, crushing, compaction, extrusion, pelletizing, dehydration, collection and other processes, which saves electricity, improves product quality, and reduces labor intensity of workers; |
6 | The simultaneous recycling of leftovers and production waste saves customers storage space; |
●Ability:
LIANDA pelletizing system with superior quality which have high
productivity for PP/PE/PS/ABS/BOPP/CPP plastic could get high
property output pellets.
●Stability:
The pelletizing system is available for 24 hours working non-stop
operation.
●Efficiency:
The pelletizing system have very low consumption values for
electricity, water and labor.
●Control:
Intelligent automatic control of pelletizing system reduces the
labor operation, makes the whole system easier and more reliable to
control.
●Service:
Consistently quick and careful service in pre-sales and after-sales
process. Overseas installation, commissioning and training are
available.