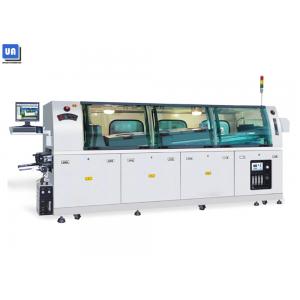

Add to Cart
Auto Feed Lead Free Automated Soldering Equipment RF 350XL Hot Air
Full Automatic Lead Free Wave Soldering Machine RF-350XL Hot Air
Basic date of wave solder RF-350XL
Model | RF-350XL |
Options available | N2 |
Top IR preheating | |
400/450 max PCB width, | |
Central support for big PCB | |
Power supply | 3P/AC 380V |
3P/AC 220V | |
Flux feeding | Auto feed |
Finger type | V, L or customized |
Conveyor width adjust | Electric control |
Conveyor width (mm) | Max 350 or customized |
Preheater | Cast aluminum plate + hot air |
Solder pot capacity (kg) | Approx. 400 |
Machine Dimension (mm) | 4500*1400*1700 |
Weight (kg) | 1920 |
Control | PC+PLC |
Preheating zone length (mm) | 1800 |
Solder pot movement | Up/down, in/out all-electric control |
Solder pot material | Titanium alloy |
Flux spray | Step motor control |
Cooling type | Forced air cooling |
Features of wave solder RF-350XL
1. Wave Soldering Machine Pneumatic components: Japan SMC pneumatic
components and other import brands,ensuring gas supply accurate and
steady.
2. Spray control: computer control or manually adjust switch.
3. Cleaning device: automatic cleaning, modular design, easy
maintenance.
4. Temperature Protection:ETA using third-party over-temperature
protection, multiple protection layers to ensure safe operation.
5. Wave Soldering Machine comply with CE, CCC, UL and other
standards and specifications.
6. Automatic board connection device, smooth and stabe.
7. A special aluminum alloy guide rail, high strength and hardness
to ensure no deformation.
8. Rodless cylinder or stepper motor drive spray head, round-trip
injection, spray area is automatically adjusted with PCB width and
speed.
9. 1800mm long four period of preheating. Infrared independent PID
temperature control, heating uniform, safe and stable.
10. 4mm SUS316 stainless stell furance, new furance design,
beautiful shape and easy to clean.
Infomation about wave solder RF-350XL
* Fluxing
Flux in the wave soldering process has a primary and a secondary
objective. The primary objective is to clean the components that
are to be soldered, principally any oxide layers that may have
formed.[3] There are two types of flux, corrosive and noncorrosive.
Noncorrosive flux requires precleaning and is used when low acidity
is required. Corrosive flux is quick and requires little
precleaning, but has a higher acidity.
* Preheating
Preheating helps to accelerate the soldering process and to prevent
thermal shock.
* Cleaning
Some types of flux, called "no-clean" fluxes, do not require
cleaning; their residues are benign after the soldering process
Typically no-clean fluxes are especially sensitive to process
conditions, which may make them undesirable in some
applications.Other kinds of flux, however, require a cleaning
stage, in which the PCB is washed with solvents and/or deionized
water to remove flux residue.
Pictures of wave solder RF-350XL