- In LED PCB manufacturing, the LED is attached to the circuit board with the help of soldering and has a chip that is used to produce light when connected to the electricity. A ceramic base and thermal heat sink are used for chip bonding.
- An LED circuit board is likely to generate much heat, and using traditional cooling methods makes it difficult to cool it. The aluminum PCBs are preferred for LED applications as they offer a high ability to thermal dissipation.
- PCBs are often found in the membrane switch for lower circuits with LED indicators because they give structural display windows. These can integrate easily into the membrane switch design of PCB, but when it comes to choosing the LED type, there are some choices to make:
1. Block and single point LED
They are the most versatile PCB LEDs. They perform well with almost every kind of finished material surface. For higher light diffusion, it is good to use a textured or matte surface.2. Surface mount or integral single point LED
These are mounted on the bottom layer of the lower circuit. They are available in an extensive color range, including bi-color.
To emboss a graphics layer to put up the LEDs, it is quite easy to terminate LEDs from the same connector tail as of the switches. LED termination is provided on the separate tail; there is no need to emboss the graphics.
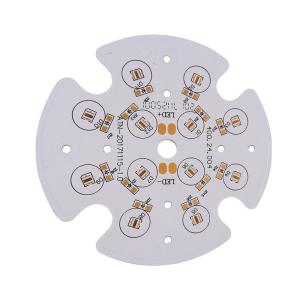
