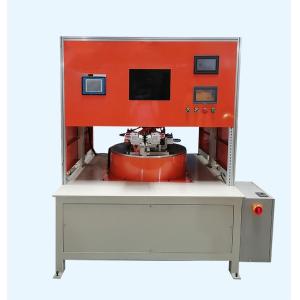

Add to Cart
Process term | Process introduction | machine | Machine size | floor space | power (Kw) | |
Length(m) | Width(m) | |||||
Process 1 | Steel Coil Laser cutting | Laser cutter line | 12000x2600x1950mm | 17 | 2.6 | 45 |
Process 2 | Sheet welding for Saving Material | Straight Seam Welding Machine | 1400x1100x2000mm | 1.4 | 1.1 | 0.4 |
Process 3 | Sheet Grinding for Saving Material | Sheet Grinding Machine | 2250x1550x1800mm | 2.3 | 1.6 | 3.2 |
Process 4 | Punching of water hole | Deep throat Press machine/J21S-40T | 1500x1200x2000mm | 1.5 | 1.2 | 4 |
Process 5 | Punching for Prebending | Deep throat press machine/J21S-63T | 1700x1400x2200mm | 1.7 | 1.4 | 4 |
Process 6 | Press the water line | Bending machine/30T-1600MM | 2600x1400x2000mm | 2.6 | 1.4 | 3 |
Process 7 | Bending of the sink base | Bending machine/63T-2500MM | 2800X1700X2350MM | 2.8 | 1.7 | 5.5 |
Process 8 | Press arc & bottom corner | Two-In-One Integrated Rolling Seam&Corner Pressing Machine | 1300x750x2000mm | 1.3 | 0.75 | 2.3 |
Process 9 | Welding for vertical seams and bottom corner | CNC Welding Special Machine | 1400x1100x2000mm | 1.4 | 1.1 | 0.4 |
Process 10 | Round corner Of vertical seams grinding (Inside) | Grinding Machine For Round corner Of vertical seams | 2550x850x2200mm | 2.6 | 0.85 | 2.3 |
Process 11 | Repair the Panel's missing corners | CNC Welding Special Machine(for panel repair) | 1100x850x1450mm | 1.1 | 0.85 | 0.4 |
Process 12 | CNC Welding For Panel's Inner Edge | Multi-Axis CNC Welding Special Machine (For panel's inner edge) | 1700x1400x1600mm | 1.7 | 1.4 | 1.3 |
Process 13 | Grinding for the sink's panel | Grinding machine (Abrasive belt type) | 2500x1400x1700mm | 2.5 | 1.4 | 3 |
Process 14 | Grinding for the sink's panel(mirror surface) | Grinding machine | 3000x1400x1700mm | 3 | 1.4 | 3 |
Process 15 | Painting For Sink Bottom Back Side | Manual painting equipment | 2200X1800X1600mm | 2.2 | 1.8 | 4.5 |
Process 16 | Drying after Painting | Drying Oven | 13000X1000X1600mm | 13 | 1 | 30 |
Total floor space(Includ spaced distance and transportation route):>65m(Length)x 10m(Width) |
Process flow | Equipment name | Specific machine name |
Cutting | Laser cutting | Customizable |
Seam and corner pressing | Seam and corner pressing machine | Seam pressing machine, Corner pressing machine, Integrated seam and corner pressing machine |
Stamping | Stamping machine | Punching of water hole,Punching of Prebending |
Bending | Bending machine | Bending to form the bowl shape, Press the water line |
Welding | Welding machine | CNC fillet welding machine, CNC corner mending welding machine,
seam welding machine, CNC planar welding machine, Press arc & bottom corner, |
Grinding and polishing | Grinding and polishing machine | Automatic Grinding for the sink's panel(Rough Polishing),Automatic Grinding for the sink's panel(Fine Polishing), Round corner Of vertical seams grinding (Inside) |
Advantages: