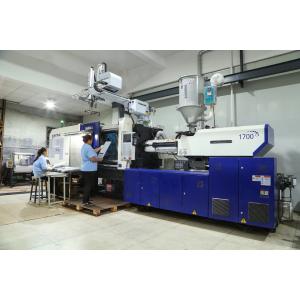

Add to Cart
Injection Molding Common Problems And Solutions
Bubbles:
Cause: The bubble is easy to occur in the part of the forming product wall thickness is thicker, the formation of the reason and the forming product sag is exactly the same. Formed on the surface of the forming product for the depression, in the forming product thick wall in the middle of the formation of the cavity for bubbles. According to the causes of bubbles, the countermeasures are as follows: when the wall thickness of the product is large, the cooling rate of the outer surface is faster than that of the center. Therefore, with the progress of cooling, the resin edge of the center shrinks and expands to the surface, so that the center is insufficient filling. This condition is called a vacuum bubble.
Countermeasure
1, according to the wall thickness, determine the reasonable gate, runner size. Generally the gate height should be 50% ~ 60% of the wall thickness of the product.
2. Until the gate is sealed, a certain amount of supplementary injection material is left.
3. The injection time should be slightly longer than the gate sealing time.
4, reduce the injection speed, improve the injection pressure, the use of high melt viscosity grade materials.
5, due to the production of volatile gas caused by the bubble, the solution is mainly: (1) full pre-drying. (2) Reduce the resin temperature to avoid the generation of decomposition gas. The bubbles caused by poor fluidity can be solved by increasing the temperature of resin and mold and increasing the injection speed.
6, warping, deformation of injection products warping, deformation is a very tricky problem. It should be mainly solved from the aspect of mold design, and the adjustment effect of forming conditions is very limited. When deformation is caused by residual stress caused by molding conditions, stress can be eliminated by reducing injection pressure, increasing mold temperature and making mold temperature uniform, increasing resin temperature or adopting annealing method.