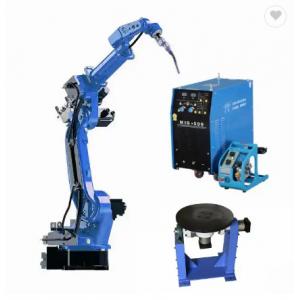

Add to Cart
6 Axis Automatic Welding Robot with CHD MIG 500 Electric Welding Machine and Welding Positioner
Ultrasonic Navigation and Positioning Technology for Mobile Robots
The working principle of ultrasonic navigation and positioning is
also similar to that of laser and infrared. Usually, ultrasonic
waves are emitted by the emission probe of the ultrasonic sensor,
and the ultrasonic waves encounter obstacles in the medium and
return to the receiving device.
By receiving the ultrasonic reflection signal emitted by oneself
and calculating the propagation distance S based on the time
difference between the ultrasonic emission and echo reception, as
well as the propagation speed, the distance from the obstacle to
the robot can be obtained. There is a formula: S=Tv/2, where T -
the time difference between the ultrasonic emission and reception;
V - The velocity of ultrasonic waves propagating in the medium.
Of course, there are also many mobile robot navigation and
positioning technologies that use separate transmitting and
receiving devices. Multiple receiving devices are arranged in the
environmental map, while transmitting probes are installed on the
mobile robot.
In the navigation and positioning of mobile robots, due to the
inherent defects of ultrasonic sensors, such as mirror reflection
and limited beam angle, it is difficult to fully obtain surrounding
environmental information. Therefore, ultrasonic sensing systems
composed of multiple sensors are usually used to establish
corresponding environmental models, and the information collected
by the sensors is transmitted to the control system of the mobile
robot through serial communication, The control system then uses
certain algorithms to process the corresponding data based on the
collected signals and the established mathematical model to obtain
the position environment information of the robot.
Due to the advantages of low cost, fast information collection
rate, and high distance resolution, ultrasonic sensors have long
been widely used in the navigation and positioning of mobile
robots. Moreover, it does not require complex image equipment
technology when collecting environmental information, resulting in
fast ranging speed and good real-time performance.
At the same time, ultrasonic sensors are also less susceptible to
external environmental conditions such as weather conditions,
ambient light, obstacle shadows, and surface roughness. Ultrasound
navigation and positioning have been widely used in various
perception systems of mobile robots.
About the company
Our guide rail has cooperated with many international well-known robot brands, such as ABB KUKA FANUC Yaskawa UR. The companies involved mainly include palletizing, loading and unloading. The load of the guide rail ranges from 500kg to 5000kg. The length of the guide rail is customized according to the needs of customers. We have made a case that an ABB IRB6700 robot corresponds to 20 CNC machines, and a 50m long guide rail completes the reciprocating motion, loading and unloading of the robot. The number of robots is greatly reduced and the integration cost is saved.
Our company also offers industrial robots at very favorable prices
to place orders together at lower prices.
Welcome to Shanghai, China, to investigate our robots and rails!
Company Product Supply
ABB robot
KUKA robot
Yaskawa robot
Fanuc robot
UR robot
Cobot
Guide rail
Cobot made in China
Product specifications
Product parameters table
Packaging and Transportation