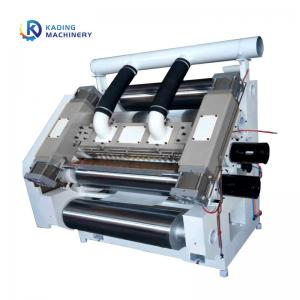

Add to Cart
Single facer machines are vital components in the corrugated cardboard manufacturing process, serving the critical function of creating the fluted medium that forms the core of corrugated board. In this article, we will explore the technological process and usage methods of single facer machines, shedding light on their essential role in the packaging industry.
Single Facer Machine Specification
Working Width | 1200mm-2500mm | |
Heating Method | Steam/Electric/Oil heating (optional) | |
Speed | 100m/min, 150m/min, 180m/min, 200m/min, 220m/min, 250m/min | |
Compress-Air Pressure | 0.4-0.9MPa | |
Flute Type | Standard flute | UV flute |
Standard spec. | A,B,C,E,F | |
Corrugated Roller Diameter | φ280mm, φ320mm, φ360mm, φ380mm, φ405mm | |
Wall Thickness | 130mm | |
Type | Fingerless/Cassette/Vacuum absorb |
*Machine's specification is subject to the final confirmation of seller and buyer.
Technological Process:
Feeding Section: The technological process begins with the feeding section, where the linerboard, which acts as the outer layers of the corrugated board, is fed into the machine. The linerboard is guided and aligned to ensure smooth and precise feeding into the subsequent stages.
Corrugation Section: In this section, the linerboard passes through the corrugating rolls. These rolls have specialized flute profiles that shape the corrugated medium. The corrugating rolls apply pressure and heat to create the distinctive wave-like pattern of the flutes, such as A, B, C, or E flutes, which determine the strength and cushioning properties of the resulting corrugated board.
Gluing Section: Once the corrugated medium is formed, it proceeds to the gluing section. Here, adhesive is applied to the flute tips of the corrugated medium using a glue applicator. The adhesive ensures proper bonding between the linerboard and the corrugated medium, forming a sturdy composite structure.
Drying and Cooling: After the gluing section, the corrugated board undergoes drying and cooling processes to facilitate adhesive curing and stabilization. These processes ensure the integrity and strength of the final corrugated board.
Usage Methods:
Set-Up and Calibration: Before starting the production, it is crucial to set up and calibrate the single facer corrugated machines properly. This involves adjusting the machine parameters, such as flute profiles, temperature, and speed, to match the desired specifications of the corrugated board. Operators must follow the manufacturer's guidelines and utilize the machine's control panel and interface to make necessary adjustments.
Material Handling: Operators need to ensure the proper feeding of linerboard into the machine. This involves aligning the linerboard correctly and monitoring the feeding process to prevent misalignment or jams that could affect the quality of the corrugated board.
Monitoring and Quality Control: During the production process, operators must continuously monitor the machine's performance and inspect the quality of the corrugated board being produced. This includes checking for consistent flute formation, proper adhesive application, and overall board integrity. Any deviations or issues should be promptly addressed to maintain optimal production quality.
Maintenance and Cleaning: Regular maintenance is essential to keep the machine in optimal working condition. This includes cleaning the machine components, inspecting and replacing worn parts, and ensuring proper lubrication. Operators should follow the manufacturer's maintenance guidelines to extend the machine's lifespan and prevent unnecessary downtime.
Conclusion:
Single facer corrugated machines follow a well-defined technological process, starting from the feeding section, through corrugation, gluing, and drying stages. Operators play a crucial role in setting up, calibrating, and monitoring the machine to ensure the production of high-quality corrugated board.
By understanding the usage methods of these machines, operators can maximize efficiency, maintain quality control, and optimize production processes. Regular maintenance and adherence to manufacturer guidelines further contribute to the longevity and reliability of these machines.
Mastering the technological process and utilization methods of these machines is essential for corrugated cardboard manufacturers, enabling them to meet the demands of the packaging industry and deliver superior packaging solutions for various applications.
Kading Company, a professional carton manufacturer with 15 years of experience, the main products are carton printing machines, carton slotting machines and carton die-cutting machines, we will do our best to give every customer the best solution.
The corrugated 48CRMO alloy steel is used, and the surface hardness of the heat treatment is above HV1200.
The corrugated roller module is separated from the entire machine,
which can be replaced by the overall lifting and replace the ascent
type at any time.
The adhesive and fixed paste are designed as a group guide track
and disassembling to shorten the maintenance time.
The main transmission of the frequency conversion motor, the
independent driver box, and the three -axis transmission, which
controls the acceleration of the corrugated machine by the
inverter, and achieves a communication interface to achieve energy
-saving effects in the future.
Both the corrugation roller and pressure roller bearing are high
-temperature lubricating fat to ensure long bearings and smooth
operation.
The closed gear transmission oil is soaked, the noise is small, the
operation is stable, and the life of the gear is long.
The host is suspended, and the glue area is rotated to avoid drying
the roller surface.
Configure the spray device to adjust the humidity of the original
paper at will.
The corrugated roller is made of special alloy steel of 48CRMO
alloy steel, and the hardness is HRC58 ° -60 °
Oil lubricating gear box, low noise and universal transmission, and
also separate power. Main motor conversion control (optional).
The vacuum suction system can provide a perfect flute shape even at
high speeds, and the explosive volume controller is equipped.
The bearings of corrugated rollers and pressure rollers are
lubricated by high temperature lubricating oil.
The surface of the bonding roller is carved and chrome -plated by
special mesh patterns. Automatic and periodic glue of glue unit.
Cangzhou Kading Carton Machinery Manufacturing Co., Ltd's factory was founded in 2009 and is located
in Dongguang County, Cangzhou City, Hebei Province.
We are a manufacturing enterprise that produces carton making machinery, with 30 expereinced workers,
2 professional product tester, and 1 core skilled carton printer engineer; Besides, we also have a sales team
composed of a group of young people with forward thinking, we can make a professional product plan for you
according to your product needs.
Our company's self-produced product lines include carton printing machines, carton die-cutting machines,
and carton slotting machines; Our advantageous products include Carton stitching machines, Folder gluer
machines, Flute laminating machines, Single facer machines, etc.
If some related products you need are not produced by ourselves, with our mature product supply chain
system, we will also help you purchase products that satisfy you with the most competitive price and the
most guaranteed quality as the standard.
In addition to our own foreign trade business, our factory also cooperates with many trading companies,
so our products are exported to dozens of countries such as the Middle East, Africa, Southeast Asia, and
the European Union, and are well received by the majority.
There are also many brand&branded manufacturers among our customers, these factories are very relieved
to entrust the production of some products to us, which is enough to show that our quality and production
conditions are trustworthy.
Cooperate with us, benefit together!
Q: Are you a factory or a trading company?
A: We are a direct manufacturer that is located in Dongguang county,
Cangzhou city. Welcome to visit our factory!
We can also have video call if you’d like an online factory tour.
Q: How do you ensure your quality?
A: 1. Trustworthy and long-term cooperative raw material suppliers;
2. Skilled&experienced engineer&workers;
3. Mature QC system;
4. Specially-assigned merchandiser;
5. Advanced production workshop.
Q: How about your after-sale service?
A: 1. Special after-sale team will be 24/7 online;
2. Can guide the installation door-to-door;
3. One-year warranty for spare parts.
Q: How many languages does your machine support?
A: Our machine supports all the languages.
Q: How long it will take to produce machine?
A: Delivery time largely depends on the machine type, for some small
machine like manual stitching machine, manual
banding machine etc, usually we have stock available.
But for the large machines like carton printing die cutting
machine, automatic stitching machine etc, it usually takes
around 35-50 days to produce.
Q: Can we visit your factory?
A: Sure, welcome to pay a visit for our factory, we will pick you up
from airport, and will provide accommodation.