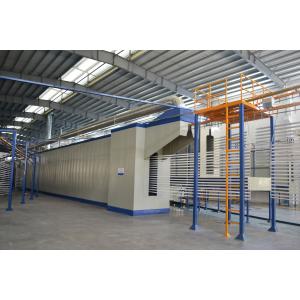

Add to Cart
600T/month Powder Coating Production Line
Major Equipment Parameter
1, Drying Oven:
(1) Technical note of moisture drying oven:
A. Moisture drying oven consists of chamber, return air piping, bottom framework, inner framework, simple fuel gas heating system and automatic temperature control system, etc.
B. Top opening (translational) oven is used for the oven, and the hot wind is delivered from bottom to the top. Air supply duct is set inside the oven.
C. Overtemperature protection switch is set to protect the combustion system. When there are the problems of overtemperature and draught fan failure, heating system can be switched off timely and sound-light alarm will be sent out.
D. Centrifugal fan, water-cooling bearings are used for circulating fan. Space is saved for maintenance in the installation site.
E. Stainless internal wall board is used in the combustion chamber, and the insulating layer is 200mm rock wool.
(2) Technical parameters of hot wind circulation oven:
No | Item | Specification | Note |
1 | Type | Hot wind circulating top-opening (translational) oven | |
2 | Effective size | 6500´2200´2200mm(Length X width X height) | Actual height is adjusted according to pretreatment pool |
3 | Processing temperature | 80~120℃ (adjustable) | |
4 | Heating up time | It reaches the setting temperature in 10-15min at a room temperature of 15℃ | |
5 | Drying time | About 300-40min required | It depends on workpiece |
6 | Heating method | Natural gas is used to heat directly with hot wind circulating convectively |
(3) Materials utilization of moisture drying oven:
Name | details | Texture |
Oven chamber | Internal wall | Galvanized sheet:δ1.2mm |
External wall | Cold-rolled sheet: δ1.2mm | |
Framework | Angle iron 25×25 | |
Rock wool thermal insulation material | δ100mm 80Kg/m3 rock wool | |
Underframe | 10# U-steel | |
Circulating air duct (built-in) | Return duct | Galvanized sheet: δ1.2mm |
Furnace door | Framework | Profile steel and A3 rolled plate |
Top panel | Cold-rolled sheet δ1.2mm | |
Bottom panel | Galvanized sheet δ1.2mm | |
Thermal insulation and thermal insulation layer | δ100mm, 80Kg/m3 rock wool | |
Heating chamber | Internal wall | Stainless steel plate: δ1.5mm |
External wall | Cold-rolled sheet δ1.2mm | |
Thermal insulation material | δ200mm 80Kg/m3 rock wool | |
Framework | Angle iron 25×25 |
(4) Outsourcing of drying tunnel equipments:
Name | Moisture drying oven | |
Combustion engine | Brand | BENTONE |
Type | BG300 | |
Combustion power | 200,000 kcal/h | |
Fire adjusting form | Single period of fire | |
Power consumption of combustion engine | About 0.18W | |
Rate of flow | 6~19 m3/h | |
Maximum pressure | 360 millibar | |
Working pressure | 20 millibar | |
Quantity | 1 set | |
Hot wind circulating fan | Brand | Foshan Yingheng Ventilator |
Power of draught fan | P=7.5KW×1 set | |
Blast volume | 8288~16576 m3/h | |
Wind pressure | 1116~1760 Pa | |
Temperature controller | PID smart automatic calculation controller | |
No. of temperature controller | E5AZ | |
Accuracy of instrument | 0.1℃ | |
Type of output control | Relay contact output AC250V.3A | |
Type of input control | Thermocouple | |
Alarm output function | Alarm output in two positions |
2, Spray chamber and recovery system:
(1) Overall scheme description:
External dimension of spray chamber: L7000mm×W1800mm×H3250mm
Structural feature: rounding top and U-bottom structural design that are used for spray chamber can make sure that the air will flow smoothly and will not cause interference in air flow, by which it will reach a high spraying rate.
1.2, Design parameters and advantage description of overall scheme
a). High-efficiency two-stage cyclone recovery system is used for the improved “HAPPY-12”, and a rotary filter element is used for recovery.
b). Stainless steel plate is used for the spray chamber with 10 automatic gun openings (5 on each side). Besides, transverse-distributed way is used for the spray guns, and a piece of gun can be distributed in each groove. Meanwhile, two manual spraying positions are configured in the system for the complicated workpiece to make up by manual.
c). Top technologies are introduced from overseas for the whirly recovery, and the recovery rate can be over 95%. The equipment has a vibrating screen system to make sure that the powder can be recycled normally without any pollution. The appearance of the whole structure is nice, elegant, sturdy and durable.
d). The improved “HAPPY-08” spray chamber has the features of being low in five aspects, which are high in three aspects and fast in two aspects (low powder consumption, low noise, low energy consumption, low powder wasted and low maintenance rate; high spraying rate, high powder recovery rate and high degree of automation; fast purification and fast color changing).
e). The whole set of spray chamber can be divided into seven major parts, which are the body of spray chamber, cyclone automatic recovery device, rotary filter element self-cleaning filtration system, automatic recovery system, powder supply bucket, general electric control system and intelligent elevator.
f). Manual plate turnover device is used for the bottom air flue of spray chamber, where world-advanced mushroom-head cleaning system is configured so that the powder can be recycled on time, and blocking powder that is caused because of being stored for too long can be reduced.
g). Human-computer interface (Chinese display) which is a simple operating system is used for the whole set of chamber that it makes human and machine combined the best, by which the intelligence degree of operation is improved.
(2) Basic configuration of spray chamber:
Part I Spray chamber | ||
Size of spray chamber | L7000mm×W1800mm×H3250mm | |
Mode of operation | Automatic and manal spray | |
Spray chamber | Improved HAPPY-08 | |
Side plates of spray chamber | δ 1.5mm stainless steel plate | |
Top board of spray chamber | δ 1.5mm stainless steel plate | |
Bottom board of spray chamber | δ2.0mm stainless steel plate | |
Maximum suspension range of workpiece inlet and outlet of spray chamber | 1800 x 300 mm (HxW) | |
Opening size of inlet and outlet of spray chamber | 2000 x 500 mm (HxW) | |
Length of spray chamber (total length) | 7000 mm | |
Width of spray chamber | 1800 mm | |
Automatic positions of spray chamber | 2×5, 10 parts in total | |
Manual positions of spray chamber | 2 | |
Manual spray operation platform | 2 | |
Cleaning device in the bottom | The advanced and pneumatic bottom plate cleaning system in spray chamber can completely overcome the high failure rate and impurity pollution to the mechanical scraper device. | |
Features | Appearance is artistic and elegant | |
Stainless steel plate is used for the spray chamber that it’s convenient and efficient to change colors, and the possibility that colors mixed caused because of dead angles not being clean can be reduced. | ||
Airflow design that is reasonable can make air flow more smoothly in the spray chamber, by which it can make sure about the powder spraying rate and coating quality. | ||
The top and sideward dustproof illuminating systems are configured so that it’s easier for operators to observe workpieces and reduce waste products because of being ignored to spray. | ||
Manual spray opening is installed in the valve that is designed specially, where operating platform is equipped so that it’s convenient to have manual spray and color changing. | ||
The design is compact that it’s convenient to have maintenance. | ||
Part II Whirly automatic separating device | ||
Air volume | 13,500 CBM/H | |
Features | a. It’s only needed to clean the bottom and sifter of whirly separator, and there are the self-cleaning functions inside and it’s unnecessary to clean. Thus, it’s more convenient to change colors, and it can also better meet clients’ requirements of changing colors. | |
b. The recovery rate is 95%~97%, and the ultrafine powder and pollutants of recycle powder can be separated and discharged to class-2 filtration system. Ultrafine powder will not be mixed into the available powder paint to cause product quality flaw. | ||
Party III Rotary filter element self-cleaning filtration system | ||
Main parts | Electric control device, filter element, rotary cleaning system, recycle powder bucket, draught fan and electric motor | |
Material | δ 3.0mm A3 plate (top-grade white powder sprayed) | |
Rotary filter element cleaning system | 8 sets | |
Filter element (imported) | 16 pieces | |
Filter efficiency | 99.99% | |
Exhaust emission load of filter | <3.0 mg/cu.m | |
Noise | <85dB | |
Motor power | 18.5KW | |
Air compression working pressure | 4.0 ~ 5.5 bar | |
Blowback gas consumption each time | 100 litres | |
Features | a. The most advanced generation-three low-abrasion rotary filter element cleaning system is used for the filter element of filter to have periodic automatic cleaning. Thus, it can make sure that the filtering area of filter element can have the most complete cleaning in the condition of lower energy consumption. | |
b. The advanced polyester filter material is used for the filter inside. It can reach 99.99% efficiency when filtering standard powder coating and the minimum exhaust discharge can be 3mg/m3. | ||
Part IV Automatic recovery system | ||
High-power recycle powder pump | 2 pieces | |
Flow | 2.KG/min | |
Vibrating screen system | Stainless steel screen | |
Part V Powder supply bucket | ||
Material | δ1.5mm top-grade white powder sprayed | |
Capacity | 150 litres | |
Input compressed air pressure | 2bar | |
Part VI general electric control cabinet | ||
Cabinet material | A3 plate (powder spray) | |
Electric control element | SIEMENS PLC is used to have centralized control, and microcomputer touch screen control system is configured. |
3, Powder spray elevator: 2 sets
PLC microcomputer control system is used for this elevator, drive motor runs under the control of frequency converter. Signals which are measured through the encoder installed on reducer shaft are sent back to PLC, and signals are sent to frequency converter from PLC when the stroke of elevator is set by manual so that the elevator can have reciprocating motion frequently in an effective coverage. Since the principle of optics is used for rotary encoder, the stroke of elevator can be more accurate and running more stable.
Device configurations below:
Powder spray elevator | |
Specification and technical data | 1. Material A3 plate 2. Effective reciprocating stroke 2200mm 3. Rated load capacity 30kg 4. Rated voltage and power: AC 220V ,750W 5. The speed is stepless adjustable, and the adjustable range is 0~30m/min 6. Rated power 1.1kw/set 7. Speed reducer: MOTOVARIO (Italy) |
Feature description |
|
4, Curing drying tunnel: 40.0´1.0´3.95m (length X width X height)
Curing drying tunnel is a ring drying tunnel that is heated directly by fuel gas. It has a set of fuel gas heating system and independent hot air circulating design.
1) Structural composition and features of curing drying tunnel:
(1) Drying tunnel consists of the main part of drying tunnel, hot air circulating system and exhaust emission system. A reasonable hot wind flow direction can be formed in drying tunnel with a reasonable layout. Besides, hot air overflowing to the workshop can also be avoided effectively, by which not only energy sources can be saved, but also environment being protected. Exhaust emission system can discharge the exhaust gas from the furnace.
(2) Tower structure is used for the drying tunnel.
(3) The blowing-in layout of hot air circulating system is up-return down-supply interconversion. Air supply outlet is set below the workpiece, and return duct is set upside the drying tunnel. A reasonable hot wind flow direction can be formed in the drying tunnel with a reasonable layout of air supply outlet and return air inlet under natural lifting power of hot air. Thus, an effect of well-distributed heating for the workpiece, good economical efficiency for air supply and reasonable air distribution can be reached. Air supply outlet is flexible and adjustable. By means of adjusting the blast capacity of air supply outlet, the air output can be changed in each stage, thereby the temperature is well-distributed in the drying tunnel. The wind adjusting plate of air supply groove is made from galvanized sheet.
(4) In order to guarantee the surface quality if workpiece, hot wind filter system is set specially. A thermal cycle air filter is set in air supply outlet that the dust produced in the cyclic process can be filtered. The filter layer is a 5-layer stainless filter net, the thickness of filter is 30mm and the initial resistance is less than 200pa. air filter is dismountable to have the operations of maintenance and ash removal. Therefore, the quality of air supply and coating can be guaranteed.
(5) In order to reduce heat output in the outlet of drying tunnel, a set of heat insulation area is set in the outlet of drying outlet to reduce energy consumption and protect the working environment.
2) Curing oven technical parameters:
No. | Item | Specification | Note |
1 | Mode | Hot air circulating cut-through curing oven | |
2 | Structure | Frame structure | |
3 | Internal size | 40000´700´3700 (length X width X height) mm | |
4 | Processing temperature | 180~220℃ (adjustable) | |
5 | Temperature rise time | It rises to the setting temperature in 30min at room temperature | |
6 | Curing time | 20min | |
7 | Temperature control measuring point | One point for control and one point for monitoring | |
8 | Heating method | Heated directly with natural and hot wind convective circulation |
3) Materials utilization of moisture drying oven:
Name | details | Texture |
Oven chamber | Internal wall | Galvanized sheet:δ1.2mm |
External wall | Cold-rolled sheet: δ1.2mm | |
External edge ornament plate | δ1.5 cold plate hydroforming | |
Internal edge ornament plate | δ1.2 galvanized sheet hydroforming | |
Framework | Angle iron 25x25 | |
Rock wool thermal insulation material | δ150mm 80Kg/ m3 rock wool | |
Underframe | Support frame | 80×50 square tube |
Bed plate | A3 plate δ10mm | |
Circulating air duct | Return duct | Galvanized sheet: δ1.2mm |
Air duct | Galvanized sheet: δ1.2mm | |
Exhaust pipe | Standard spiral duct | |
Heating chamber | Internal wall | Stainless steel sheet: δ1.5mm |
External wall | Cold-rolled sheet: δ1.2mm | |
Thermal insulation material | Outerδ200mm 80Kg/m3 rock wool | |
Framework | Angle iron 25×25 |
4) Outsourcing of drying tunnel equipments
Name | Curing oven | |
Combustion engine | Brand | BENTONE |
Type | BG400-2 | |
Combustion power | 300,000 kcal/h | |
Fire adjusting form | Double period of fire | |
Power consumption of combustion engine | About 0.25KW | |
Rate of flow | 6~31.8m3/h | |
Maximum pressure | 360 millibar | |
Working pressure | 20 millibar | |
Quantity | 2 sets | |
Hot wind circulating fan | Brand | Foshan Yingheng Ventilator |
Power of draught fan | P=7.5KW×2 sets | |
Blast volume | 8288~16576 m3/h | |
Wind pressure | 1116~1760 Pa | |
Temperature controller | PID smart automatic calculation controller | |
No. of temperature controller | E5AZ | |
Accuracy of instrument | 0.1℃ | |
Type of output control | Relay contact output AC250V.3A | |
Type of input control | Thermocouple | |
Alarm output function | Alarm output in two positions |
5, Suspension conveying system
(1) Conveyor is installed with emergency shut-down device in the corresponding operating position for the convenience of operating production running to ensure safety.
(2) Conveyor line driving device is used for planet cycloidal pin gear speed reducer and electric motor. The chain is driven by driving chain, and driving device has the functions of phase loss, overload and shirt circuit so as to make the running of conveyor line safer and more reliable.
(3) The type of control is frequency control, which can meet the requirements of different manufacturing techniques and speeds.
(4) The operation of conveyor is stable, and there is not the problem of crawl or block.
(5) The rail surface of trolley conveyor is painted, and the colors are decided according to the requirements of clients.
(6) Valid parameters of conveyor
Conveyor No. | QXT-250 chain (Taiwan Zhurong) |
Rail specification | T4.0×80×80 (carbon steel) |
Horizontal cornering | R2500 manganese steel |
Single-point load | 50KG |
Pitch | 250mm/section |
Driving device | Motor P=3.0KW×1 set Speed reducer 100# 60:1×1 set |
Drive seat | Conveying belt, pressing plate and bearing, etc |
Support | T2.5×100×100 square tube |
Joint | Flange |
Tension device | Heavy punch |
Lubricating device | Automatic oiling machine |
Safety device | Automatic overload protection is set Scram buttons are set in the feeding and blanking areas and spraying chamber |
6. Electrical control system
1) All the circumscribed control circuits are routed by metal sleeves or flame retardant plastic sleeves. The circuits have fastening structures to reach safety norms in utilizing electric power.
2) The control panel is under centralized control, and will be installed in the most appropriate position considered by Party A for the convenience of operation.
3) Digital display automatic controller is used for the temperature control in heating positions. Automatic control will be conducted accurately when displaying all the hot-spot temperatures.
4) Human-computer interface and PLC programming are used for the panel to have centralized control. The measures of instruments must be accurate, and the measurement error must be in the range of national standard.
5) The design, type selection, manufacturing and installation of electrical equipments must live up to the national related standards.
6) Wires should have a firm touch with the terminals of electric appliance.
7) Wires should be marked with distinct wire sizes in the positions of electrical appliance terminals and line banks. Besides, it should not be easy to be worn away or fading.
8) Combustion safety protection system is set, that’s to say, the furnace will be shut down automatically when the temperature is too high, controlled by sound-light alarm and interlocking electric devices.
9) High-quality elements produced by national appointed manufacturers are used for the control panel.
10) Spraying plastic cabinet is used for the control cabinet.
11) Power configuration form: 380V, 3-phase, 5-wire, AC
12) In the process of production, the device should have the corresponding interlocking protection and necessary alarm indication function under the circumstance below:
A.Drying tunnel overtemperature control
B.Fuel gas heat exchange firing
C.Emergency shut down
D.Heat exchanger overtemperature alarm
System control function:
1. | Combustion engine flame control system | |
2. | Curing oven temperature display and control system | Temperature display system |
Temperature control system | ||
3. | Curing oven air curtain device system | |
4. | Conveyor frequency conversion system | |
5. | Exhaust emission system | |
6. | Spraying chamber, recovery system, powder delivery and other valve systems | |
7. | PLC automatic blowback system | |
8. | Mictocomputer touch screen control system is configured |
Materials for the main electronic control system
No. | Name | Brand |
1 | Disconnector | SCHNEIDER |
2 | Contactor | SCHNEIDER |
3 | Thermal overload protector | SCHNEIDER |
4 | Intermediate relay | |
5 | PLC | SIEMENS |
6 | Touch screen | SCHNEIDER |
7 | electric lift frequency converter | Japanese MITSUBISHI |
8 | Curing oven driving frequency converter | Alpha |
9 | Indicator light and button switch | SCHNEIDER |
10 | Curing oven temperature-controlled meter | Japanese OMRON |
11 | Water-drying temperature-controlled meter | Japanese OMRON |
12 | Wire | National standard |