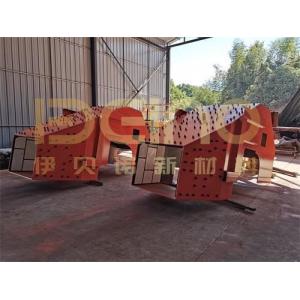

Add to Cart
Product Description
As an essential transportation device in the material conveying system, the alumina ceramic chute is the main equipment for conveying and loading materials in crushing systems such as cement, steel, coal power plants, and mines.
Steel plants and coking plants use iron ore, coking coal, and coke as raw materials to transport raw materials for the next process; they use a 24-hour cycle work cycle, and the flow of iron ore, coking coal, and coke is large, and the conveying time is long. It is easy to cause serious wear to the output equipment, especially the chute; it is often forced to stop for repairs during production, and some chute installation positions are in the air at a height of more than ten meters or tens of meters, so it is more troublesome to remove and replace; The wear resistance and impact strength of the lining material are particularly important. The installation of lining materials suitable for different site conditions can speed up the conveying of raw materials and make them durable, which is the key to realizing safe production, energy saving, and efficiency enhancement.
The wide application of alumina ceramic chutes reduces the number of maintenance and emergency repairs due to the material of the lining plate, prolongs the service life of the chutes, increases the economic benefits of enterprises, and is an effective way for safe production.
Performance Analysis of Wear-Resistant Liners for Chutes with Different Materials
NO | Texture of material | Comparison and Analysis of the Properties of Different Materials of Wear-resistant Lining Plates |
1 | High manganese steel lining plate | Advantages: Under strong impact and extrusion conditions, the surface layer can rapidly undergo work hardening, and the surface hardened layer has good wear resistance. Disadvantages: High manganese steel is very easy to work and harden, so it is difficult to machine. Most of them are castings, and a small amount of them are processed by forging. The wear resistance is general for nonimpact working conditions. |
2 | High chromium cast iron lining plate | Advantages: High chromium cast iron is an excellent wear-resistant material with high hardness and good wear resistance, and its hardness is between HRA70-80. Disadvantages: unable to cut, difficult to weld, unable to withstand the high load impact of materials. |
3 | Alloy steel lining plate | Advantages: alloy steel has higher strength and toughness than carbon steel. The hardenability of alloy steel mainly depends on the carbon content, which is slightly improved compared with carbon steel with the same carbon content. The alloy steel also has good thermal hardness and other special properties, such as heat resistance, corrosion resistance, wear resistance, and magnetism Disadvantages: It is difficult to weld, and the manufacturing cost has a certain impact. The hardness of the general alloy lining plate is difficult to exceed HRA60, which is limited in the heavy wear industry. |
4 | Cast stone liner | Advantages: Cast stone is a kind of silicate crystal material processed. It can be divided into ordinary cast stone lining plates and microcrystalline cast stone lining plates according to the different production processes and formulas. The production process of cast stone lining plate is simple, the price is low, and the hardness is high. Its wear resistance is several to ten times higher than steel plate and cast iron. Disadvantages: cast stone products have poor toughness, high hardness, and are difficult to cut. They have poor toughness and impact resistance and are rarely used in heavy-wear industries. |
5 | Polyethylene wear-resistant plate | Advantages: polyethylene polymer material has good wear resistance, good sliding properties, low friction coefficient, corrosion resistance of insulation, light texture, and easy processing, as well as good shock absorption, sound attenuation, low noise, and other characteristics. Disadvantages: low surface hardness and thermal deformation temperature, poor bending strength, and creep performance, unable to withstand large impact, and limited use in high temperature and heavy wear conditions. |
6 | Ceramic Pilates | The chute wear-resistant ceramic lining plate is the most widely used and effective chute wear-resistant material at present. Aluminum oxide is the main raw material, and its hardness reaches HRA88, second only to diamond. After adding zirconia to make ZTA ceramics, it can also have strong impact resistance, and its service life can reach more than 10 times that of manganese steel under heavy wear conditions. |
Alumina ceramic chute installation process
1. Pre-lay the wear-resistant ceramic lining plate according to the working conditions of the workpiece and the shape of the workpiece, mark the sequence number, and punch according to the position of the sequence number.
2. Grind the surface to be bonded to remove rust and oil. If there is a lot of oil, Need to be cleaned. If the bonding surface is non-metal, the surface should be polished and roughened. Special workpieces must be sandblasted.
3. Preparation of ceramic glue: The principle of mixing ceramic glue is small and several times. Note that the mixed ceramic glue cannot be placed in the air for a long time, and it is easy to deteriorate; according to the mass ratio of 2:1, mix the glue evenly; pay special attention to If the temperature is lower than 10 ℃, the heating and curing method should be adopted, and the surface to be bonded should be heated to about 30 ℃, glued and bonded, and heated until cured. We found in the construction that if no heating measures are taken, especially when the temperature is lower than 0°C, the glue is easy to freezes, and the surface appears to be cured, but there is no adhesive strength, so it is easy to detach during use, but the heating temperature It should not exceed 50 °C, otherwise the glue will react violently and bubbles will appear, which will affect the bonding strength.
4. When smearing the surface of the object to adhere, the glue coating layer should be about 1mm and should not be too thick, to ensure full filling between the ceramic lining plate and the parent body; when the corners and other cross-sections are pasted, the side wall lining plate covers a lot of the ground lining plate at 50%.
5. After the paste is completed, tap one by one with a rubber hammer and confirm that there is no empty drum phenomenon. After curing at room temperature for 8 hours, use a small hammer to lightly tap to check to see if there is a lack of glue. If there is, it can be partially removed in time. , rebounding. If the bonding surface is metal in the rainy season or a high-humidity environment, glue should be applied immediately after grinding to prevent rust.
6. Finally, tighten the ceramic lining plate and the steel parts with bolts.