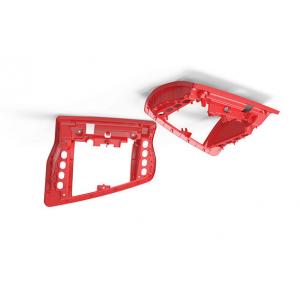

Add to Cart
Vacuum Casting Rapid Prototyping And Vacuum Casting Service For Custom Parts
Summary:
Should you choose vacuum casting for your prototyping needs? Here
is everything you need to know about the process.
In the world of rapid prototyping, vacuum casting is a valuable
technique, which can complement other processes, like CNC machining
and 3D printing, or be used independently to advance product
development with high-quality prototypes. There are many reasons to
use it for rapid prototyping applications. Keep on reading to find
out if the process is right for you.
Polyurethane vacuum casting is a specialized technique for making
high-fidelity copies of master patterns using inexpensive silicone
molds and pourable casting resins. Copies made in this way
demonstrate the same quality as plastic injection molded parts
while taking only a fraction of the time and expense to produce.
What is the process of vacuum casting?
The process starts by placing a two piece silicone mold in a vacuum
chamber. The raw material is mixed, degassed and then poured into
the mold. The vacuum is then released and the mold removed from the
chamber. Finally, the casting is cured in an oven and the mold
removed to release the completed casting.
Why Choose JYH for Vacuum Casting Services?
When it comes to vacuum casting, there are a number of
manufacturers to choose from. Choosing the right one is essential
for getting exactly the results you expect. Here are several
reasons to choose JYH for your vacuum casting needs.
Quality shouldn’t have to come at the expense of speed, and vice
versa. At JYH, we combine our extensive experience with the
industry’s latest tools and technologies to deliver high-quality
vacuum casting services on short timelines (typically in 7 to 14
days).
Vacuum casting isn’t all we do. As your one-stop production shop,
we also offer a wide range of complementary finishing services to
help your product come to life. Our finishing services include
machining, media blasting, printing, painting and more.
Your needs are unique — and you don’t want to pay for more than you
need. That’s why we never require a minimum order volume or minimum
dollar value for our vacuum casting services. We also use
state-of-the-art AI quotation algorithms for fast, accurate quotes
in 24 hours or fewer for nearly all projects.
As vacuum casting is often used for prototyping, we know that many
of the products we work on haven’t reached their final design. To
help them get there, we provide detailed design for manufacturing
support to our clients. (We can even make your patterns for you.)
We also offer detailed video files showing all production steps for
clients who can’t visit us in person.
Vacuum Casting Process:
Step 1. Master Patterns |
|
Step 2. Making the Molds |
|
Step 3. Casting Copies |
|
Vacuum Casting Tolerances
The finished dimensions of vacuum cast parts are dependent on the
accuracy of the master pattern, the part’s geometry and the type of
casting material used. Generally a shrinkage rate of 0.15% is to be
expected.
Casting molds are made from liquid silicone. This silicone is
poured around the master pattern inside of a casting box, and then
allowed to cure in an oven for 16 hours. Once dried, the mold is
cut open and the master removed, leaving behind an empty cavity in
the exact negative shape of the original.
First the pattern must be carefully prepared, and that means
sanding and sealing the surface with primer. Once it’s ready, it’s
placed into a casting box and liquid silicone is poured around it.
Depending on the size of the part, it can take 12 hours to fully
cure inside of an oven. Once dried, the mold is cut open and the
master removed, leaving behind an empty cavity in the exact
negative shape of the original.
JYH is your best partner of Vacuum Casting Rapid Prototyping And
Vacuum Casting Service For Custom Parts!