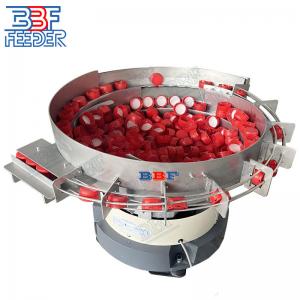

Add to Cart
Conveyor System Vibratory Bowl Feeder Crown Lids Flip Top Cap Vibrating Feeder Linear
1 . Descriptions:
Vibratory bowl feeders are vital components used across various industries to efficiently sort and orient parts. This article explores the essential steps and considerations involved in their design.
Step 1: Understanding the Components
Before diving into the design process, it is crucial to grasp the
fundamental components of a vibratory bowl feeder:
Bowl: Made of stainless steel, the bowl serves as a receptacle for
parts, featuring a helical track or multiple tracks to guide and
orient them.
Drive Unit: Comprised of an electromagnetic coil and a spring
system, the drive unit generates vibrations that propel the
movement of parts.
Controller: The controller regulates vibration frequency and
amplitude, providing precise control over the feeding process.
Step 2: Determining Part Characteristics
To design an efficient vibratory bowl feeder, thorough
consideration of part characteristics is essential. Key aspects to
consider include:
Size and Shape: Irregularly shaped or sized parts may require
special considerations in the bowl design to ensure accurate
orientation.
Material: Different materials have varying friction coefficients
and respond differently to vibrations, affecting part movement and
alignment within the bowl.
Weight: Part weight determines the intensity of vibrations
required. Heavier parts necessitate more powerful movements, while
lighter parts require gentler motion.
Step 3: Selecting Bowl Geometry
Bowl geometry plays a critical role in the design process.
Important factors to consider include:
Bowl Shape and Size: Optimal performance requires selecting an
appropriate bowl shape and size that align with the parts being
fed, ensuring a smooth and consistent flow. Consider the bowl's
size relative to part dimensions to avoid inefficient feeding or
jams.
Track Configuration: Determine the number and arrangement of tracks
within the bowl based on desired orientation and feeding rate.
Slope Angle: The angle of the bowl's slopes influences part
movement. Steeper slopes may be necessary for achieving faster
feeding rates.
Track Width and Depth: Choose dimensions that accommodate part size
while preventing jams or clogs.
Designing a vibratory bowl feeder requires careful consideration of its components, part characteristics, and bowl geometry. By following the outlined steps in this article, one can ensure an effective and efficient feeder that sorts and aligns parts for subsequent processing or assembly.
2 . Specifications:
Product name | Vibratory Bowl Feeder |
Material | Aluminum(AL7075), Stainless Steel(SUS304) or Based on Customers' Requirements |
Controller | CUH,Sanki,Sinfonia,REO,Afag |
Voltage | 220V 50HZ/110V 60Hz or Based on Customers' Requirements |
Power | 300W/500W/1000W/1500W/2000W |
After-sales Service Bowl Finishing | Spare Parts and Technology Support |
Speed | Based on Customers Requirements |
Warranty | 2 Years |
Certification | CE, ISO9001, ROHS |
Lead Time | 3 Working Weeks |
3 . Designing an Efficient Vibratory Bowl Feeder:
Vibratory bowl feeders are essential in the sorting and orientation of parts in various industries. This article outlines the key steps in designing these feeders, emphasizing important considerations at each stage.
Step 1: Components Understanding
To start, it is crucial to grasp the fundamental components: the
bowl, drive unit, and controller. The bowl acts as a receptacle
with tracks to guide and orient parts effectively. The drive unit
generates vibrations, while the controller regulates the frequency
and amplitude of these vibrations.
Step 2: Part Characteristics Determination
Consider different part characteristics such as size, shape,
material, and weight. Irregularly shaped parts may require specific
design considerations for accurate orientation. Take into account
the friction coefficients of various materials and how they respond
to vibrations, as this affects part movement and alignment.
Step 3: Bowl Geometry Selection
Selecting the right bowl geometry is vital for optimal performance.
Ensure proper alignment between the bowl and the parts, allowing
for a smooth and consistent flow. Determine the appropriate track
configuration, slope angle, and dimensions to prevent jams and
ensure efficient feeding.
Step 4: Base Unit Design
The base unit houses electromagnetic coils responsible for
generating vibrations. Choose the appropriate drive unit type based
on the application's specific requirements, such as half-wave,
full-wave, or high-speed electromagnetic drives. Additionally,
select a spring system that balances the force exerted by the
coils, ensuring stable and reliable vibration.
Step 5: Controls Implementation
Implement a control system to regulate the frequency and amplitude
of the vibrations. The control system should have variable settings
to accommodate different parts and feeding requirements. Consider
integrating feedback mechanisms, such as sensors or monitoring
systems, to enable real-time adjustments.
Step 6: Testing and Optimization
Thoroughly test the feeder's performance against the desired
specifications. Fine-tune various parameters, including vibration
settings and track geometry, to achieve optimal feeding. It is also
crucial to conduct stress testing under different loads and
conditions to identify and address potential issues.
In conclusion, designing a vibratory bowl feeder involves understanding part characteristics, selecting appropriate bowl geometry, designing the base unit, implementing controls, and conducting thorough testing and optimization. Continuous monitoring and maintenance are essential to ensure long-term performance and meet the specific needs of different applications.
4 . More Pictures: