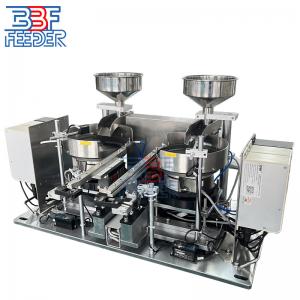

Add to Cart
CNC Vibrating Bowl Feeder Spare Parts Linear Feeding Bowl Vibration Plate
1 . Descriptions:
Efficient part handling is crucial in the realm of automated assembly and manufacturing. One versatile tool that plays a vital role in this domain is the Vibratory Bowl Feeder. This device is designed to reliably orient and feed parts from bulk, significantly enhancing production efficiency and accuracy when coupled with well-crafted tooling design.
Customization for Optimal Performance:
Tooling design is not a one-size-fits-all approach. It requires a
deep understanding of the parts' characteristics and the specific
requirements of the assembly process. Engineers often go through
prototyping and testing phases to fine-tune the tooling for optimal
performance.
Factors to Consider in Tooling Development:
Part Geometry: The tooling surfaces must align with the parts' geometry to control and guide their motion. Complex or unique part shapes may necessitate specialized tooling. 3D profiling of parts can assist in customizing the geometry.
Selection Method: The selection method employed can vary, and the tooling is shaped accordingly. Mechanical tooling and precise air jets are commonly used for selecting many components, while others may require pre-orientation through tooling and final orientation using sensors or vision sensors.
Feed Rates: The required feed rate can influence the tooling selection. Higher rates may require multiple selection passes and merging of oriented parts. Attention must be given to the clearance of selection tooling to prevent part jamming in faster running bowls.
Simplicity of Design: Complex tooling with numerous custom parts can increase manufacturing costs. Simpler modular tooling is easier to maintain and reconfigure.
Materials: The bowls can be installed in various environments, necessitating the use of suitable materials. Pharmaceutical applications, for example, may require high-grade stainless steels and closer attention to the level of finish compared to industrial applications.
Noise/Impact Reduction: Excess noise may indicate that parts are impacting surfaces too hard. Durable linings, such as polyurethane, can be added to dampen impacts and reduce noise.
Coatings: Specialized coatings like titanium nitride can improve wear resistance and prevent galling, extending the service life of the tooling in heavy-duty applications.
By considering these factors and experimenting with different tooling configurations, manufacturers can achieve optimal performance from their vibratory bowl feeding systems. Tooling design is an art that requires experience and testing to master. However, with the right tooling, vibratory bowls become highly flexible and efficient parts feeding solutions.
2 . Specifications:
Product name | Vibratory Bowl Feeder |
Material | Aluminum(AL7075), Stainless Steel(SUS304) or Based on Customers' Requirements |
Controller | CUH,Sanki,Sinfonia,REO,Afag |
Voltage | 220V 50HZ/110V 60Hz or Based on Customers' Requirements |
Power | 300W/500W/1000W/1500W/2000W |
Material Speciality | Excellent Processing Properties,High Strength, High Hardness |
Speed | Based on Customers Requirements |
Warranty | 2 Years |
Certification | CE, ISO9001, ROHS |
Lead Time | 3 Working Weeks |
3 . Maintaining and Servicing Vibratory Bowl Feeders:
Vibratory bowl feeders are essential tools in various manufacturing processes, serving industries such as automotive and electronics by efficiently sorting, orienting, and feeding components. However, like any machinery, they require regular maintenance to ensure optimal performance and uptime.
Routine maintenance should be conducted on a daily, weekly, and monthly basis by operators. This includes inspections and cleaning. Additionally, more complex preventative maintenance tasks should be carried out annually by qualified technicians.
During the annual service, experienced technicians disassemble major components and conduct a detailed inspection. They look for visible signs of wear, damage, or loose components, such as cracks, deformities, or excessive wear on the bowl surface. Springs, bolts, and other fasteners are checked for fatigue or degradation. This visual assessment provides an initial overview of the feeder's condition.
Specific tasks during the annual service include thorough cleaning of components, repair or replacement of worn or damaged elements, upgrading outdated or failing components, and performing calibrations and test runs to meet OEM specifications. This comprehensive service ensures that the feeder bowl operates at peak efficiency and minimizes the risk of breakdowns. Technicians may also suggest upgrades, repairs, or design improvements as needed. These may include replacing worn bowl liners and cradles, relining and resurfacing the bowl, refurbishing or replacing drive coils and mechanisms, and repairing or replacing worn or damaged tooling.
In conclusion, by performing annual service procedures, manufacturers can maximize uptime and minimize unplanned downtime on the factory floor. The costs of preventative maintenance are far outweighed by the expenses and production impacts of unexpected equipment failures.
4 . More Pictures: