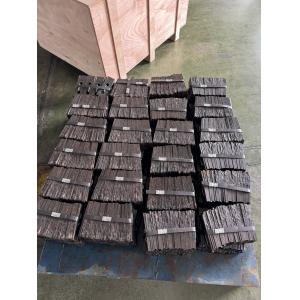

Add to Cart
Products Introduction:
Hammer mill beaters play a crucial role in the grinding process
within hammer mills, which are widely used in various industries
for material processing. These beaters are designed to crush and
grind materials fed into the mill, ensuring efficient and effective
size reduction.
Functionality of Hammer Mill Beaters
Mounted on rotating shafts, hammer mill beaters operate at high
speeds, delivering powerful strikes to the material. As the shaft
rotates, the beaters collide with the input material, breaking it
down into finer particles. This action is vital for achieving the
desired particle size and ensuring that the material is processed
correctly.
Importance of Beater Design
The design of the beaters significantly influences the overall
performance of the hammer mill. Key factors include:
Wear and Maintenance Considerations
The beater is the most susceptible component to wear in a hammer
mill. Regular inspection and maintenance are essential to ensure
optimal performance. Signs of wear can include reduced efficiency
and inconsistent particle sizes, indicating that it may be time to
replace or repair the beaters.
The machining accuracy of high-speed-running beaters is critical
for maintaining rotor balance. An unbalanced rotor can lead to
operational issues, including increased vibration and reduced
lifespan of the hammer mill. Therefore, precision in the production
of beaters is not just about performance; it is also about ensuring
the longevity of the entire milling system.
What materials are hammer mill beaters typically made from?
Hammer mill beaters are typically made from a variety of materials,
each chosen for its specific properties to enhance performance and
durability. Common materials include:
High Carbon Steel: Known for its toughness and wear resistance, high carbon steel is a popular choice for beaters. It can withstand high-impact forces.
3. Stainless Steel: Used in applications where corrosion resistance is essential,
stainless steel is durable and maintains hygiene, making it ideal
for food processing.
4. Tungsten Carbide: For extreme wear resistance, some beaters are coated or made from
tungsten carbide. This material is particularly effective in
high-abrasion environments.
5. Cast Iron: While less common, cast iron beaters may be used for certain
applications due to their good wear resistance and ability to
absorb shock.
The choice of material depends on the specific application, the
type of material being processed, and the desired lifespan of the
beaters.
How does the hardness of the beater material affect its lifespan?
The hardness of the material used for hammer mill beaters
significantly impacts their lifespan and overall performance.
Here’s how hardness influences durability:
Wear Resistance: Harder materials tend to resist wear and abrasion better than softer ones. In high-impact environments, such as those in hammer mills, a harder beater will sustain less damage over time, leading to a longer operational life.
Shanbao Machinery's Hammer Beater's Parameter
This product is ideal for those looking for a reliable and
long-lasting material due to its high striking resistance. It is
made of an alloy specially treated to create high corrosion and
wear resistance. Furthermore, it has excellent heat resistance,
making it perfect for high temperatures. It boasts outstanding
fatigue resistance, enabling it to stay tough and intact, even when
exposed to repeated impact and stress.
Raw material | Q345 Low Alloy High Strength Structural Steel |
Surfacing hardening material | Casting tungsten carbide |
Overlay cladding hardness | ≥ HRC 65 |
Substrate hardness | ≥ HRC 50 |
Group and additional weight deviation | <5g |
Weight of surfacing material | Agreement between supplier and buyer |
Special tailor-made | Support |
Length | Based on the customer’s need to customize |
Thickness | 3-10mm |
Aperture | Above 13mm |
Carburizing depth | 0.8-1.2mm |
Packing:
Production Process:
Exhibition: