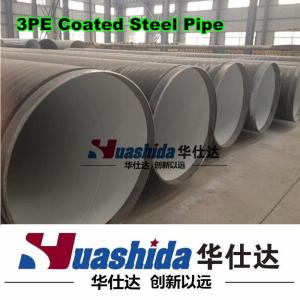

Add to Cart
Steel Pipe Anticorrosion Process Liquid Epoxy Spraying Coating and 3 Layer HDPE Coating Process
Product description
Polyurethane spraying polyethylene wrapping pre-insulated pipe
production line is used for the production of polyurethane
prefabricated direct buried thermal insulating pipes, which are
widely used in the field of heating, cooling and crude oil
transportation.
The polyurethane sprayed polyethylene thermal winding insulation
pipe production line independently developed by Huashida, consists of three parts: External shot blasting and derusting production line, polyurethane spraying
production line, and PE winding production line. The line has a number of national patents, and the third-party standardized
evaluation report has a technology advanced level of 5, reaching
the domestic leading level. And won the first set of technical
equipment in Shandong Province.
The line adopts continuous spraying production process. High automatic, fast production efficiency, saving raw materials, increased
foaming and closed cell rate, lower water absorption rate, trinity
molding, and more reliable performance. Products with low carbon
environmental protection have higher economic and social benefits.
Pipe structure
Rigid polyurethane spraying polyethylene winding prefabricated
directly buried insulation pipe consists of steel working pipe,
spraying polyurethane rigid foam insulation layer and winding
polyethylene outer protective pipe. See the following figure for
product structure
Technological flow:
Technological flow of the polyurethane coating steel preinsulated pipe equipment:
1. Remove rust from steel pipe surface
2. preheat the steel pipe to get it ready for polyurethane spraying
3. Spray polyurethane evenly on steel pipe outer surface
4. Wrap melted HDPE strap around the PU foam
5. Trim the pipe ends
Features of the polyurethane spraying PE winding insulation pipe
(1). Density, thermal conductivity, compressive strength and other
indices of the polyurethane insulation layer are uniform and
consistent. Therefore overall performance of the pipe is superior.
(2). The polyurethane insulation layer is formed by free foaming.
Since polyurethane is foamed perpendicular to the axial direction
of the pipe, compressive strength of the insulation layer is
improved.
(3). The polyurethane insulation layer is formed after spraying. The raw materials are sprayed onto the outer surface of the steel
pipe in a liquid form, and then begins to foam. Due to the high
reaction activity of the spraying polyurethane raw materials,
adhesion between steel pipe surface and polyurethane foam layer is
stronger.
(4).Roughness of the surface of polyurethane foam layer is more
conducive to increase bonding effect between insulation layer and
outer HDPE protective layer.
(5). Polyurethane insulation layer can be sprayed according to the
thickness required by customers with a thickness of 15-20mm. Costs can be significantly saved.
(6). Prefabricated directly buried insulation pipes produced using
the "spray winding" process, with polyurethane insulation layer and
polyethylene outer protective layer thickness adjustable according
to users needs. The production process does not require additional
molds and tooling, making it simple and easy to operate. Due to the
absence of expansion stress on the polyethylene outer protective
layer during foaming in the "spray winding" process, thickness of
the polyethylene outer protective layer can be relatively thinner,
reducing costs for customers.
(7). The polyethylene outer protective layer is formed by
circumferential winding, therefore circumferential elongation and
tensile strength are significantly improved. Circumferential
strength of polyethylene protective layer is stronger.
(8). As this is a completely automatic production line, Production
speed is improved and production quality is consistent and
superior.
Other supplier racks
The integrated welded structure, without adjustment devices, cannot
be installed when the ground is uneven. The height of the stand
cannot be adjusted, resulting in uneven rolling of steel pipes on
the stand, too fast rolling, or difficult rolling, which poses a
safety hazard.
Main accessories
No. | (DN) | The thickness of the insulation layer | Outer casing dia. | Min. thickness of the outer casing |
1 | 500 | 30-60 | 598-658 | 4.5 |
2 | 600 | 30-60 | 700-760 | 5.0 |
3 | 700 | 30-60 | 790-850 | 5.0 |
4 | 800 | 30-60 | 891-951 | 5.5 |
5 | 900 | 30-60 | 992-1052 | 6.0 |
6 | 1000 | 30-60 | 1093-1153 | 6.5 |
7 | 1100 | 30-60 | 1194-1254 | 7.0 |
8 | 1200 | 40-100 | 1316-1436 | 8.0 |
9 | 1400 | 50-100 | 1538-1678 | 9.0 |
10 | 1620 | 50-100 | 1738-1840 | 10.0 |