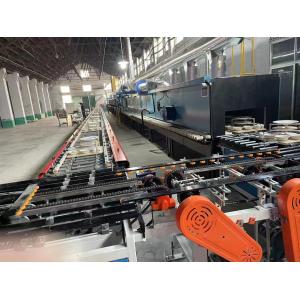

Add to Cart
Roller hearth kilns are specialized thermal processing equipment designed for the efficient and uniform sintering of advanced materials. These kilns have become indispensable in industries ranging from ceramics and glass to metallurgy and electronics due to their ability to handle a wide range of materials with precision and consistency. The roller hearth design allows for continuous operation, making it ideal for high-volume production environments where reliability and repeatability are critical. With the capability to precisely control temperature profiles and atmosphere conditions, roller hearth kilns provide manufacturers with the flexibility needed to meet stringent quality standards.
Unlike batch kilns, which process materials in discrete batches, roller hearth kilns operate continuously. Materials are loaded onto rollers that move them through various heating and cooling zones, allowing for a seamless transition between different stages of the sintering process. This continuous movement not only enhances throughput but also ensures a more uniform heat distribution across the material being processed.
Depending on the application, the kiln can be adjusted to maintain specific gas compositions, such as nitrogen or oxygen-free environments, which are crucial for certain materials like electronic ceramics. Additionally, the ability to adjust heating rates and cooling schedules gives manufacturers unparalleled control over the microstructure and properties of the final product.
Advanced insulation materials and sophisticated burner systems work together to minimize temperature variations within the kiln, ensuring consistent results. This level of uniformity is essential for producing high-quality materials with predictable performance characteristics.
Automated loading and unloading systems, coupled with real-time monitoring and feedback controls, streamline operations while reducing the potential for human error. These features contribute to improved efficiency, lower operational costs, and higher overall productivity.
Roller hearth kilns find applications across a broad spectrum of industries due to their versatility and adaptability.
these kilns are used for firing everything from traditional pottery to advanced technical ceramics required in aerospace and automotive components. Their ability to achieve high temperatures with excellent uniformity makes them ideal for producing ceramics with superior mechanical strength and thermal stability.
roller hearth kilns are employed for processes such as annealing, hardening, and tempering of metals. The controlled atmosphere within the kiln prevents oxidation and decarburization, preserving the integrity and enhancing the properties of the metal parts. This is particularly important in the production of high-performance alloys and tool steels.
Electronics manufacturing benefits greatly from roller hearth kilns, especially in the production of substrates, insulators, and resistors. The precise temperature control and atmospheric regulation offered by these kilns are crucial for achieving the exact electrical and physical properties required for these components. Furthermore, the ability to scale up production without compromising on quality makes roller hearth kilns an attractive option for electronics manufacturers.
1. What materials can be processed in roller hearth kilns?
Roller hearth kilns are suitable for a wide array of materials, including ceramics, metals, glasses, and composites. The specific suitability depends on the material's thermal and chemical properties as well as the desired end-product characteristics.
2. How does the atmosphere inside the kiln affect the sintering process?
The atmosphere within the kiln can significantly influence the outcome of the sintering process. For instance, an inert atmosphere prevents oxidation, which is crucial for maintaining the purity and enhancing the properties of sensitive materials like electronic ceramics.
3. What maintenance is required for roller hearth kilns?
Regular maintenance includes checking and replacing worn-out rollers, cleaning the burners, inspecting insulation for degradation, and updating software for automated systems. Preventive maintenance is vital for ensuring the longevity and reliability of the kiln.
4. Can roller hearth kilns accommodate varying sizes and shapes of materials?
Yes, roller hearth kilns can be configured to handle materials of different sizes and shapes. Adjustable settings for the speed of the rollers and the dimensions of the heating zones allow for customization according to the specific requirements of the material being processed.
5. What safety measures should be considered when operating roller hearth kilns?
Safety considerations include proper ventilation to manage emissions, personal protective equipment (PPE) for operators, emergency stop systems, and regular training for staff on safe operating procedures. Ensuring compliance with local regulations and guidelines is also imperative.
Roller hearth kilns stand out as a versatile solution for advanced material sintering, offering unmatched precision, efficiency, and scalability. As industries continue to demand higher quality materials with more complex properties, the importance of roller hearth kilns in meeting these demands cannot be overstated.