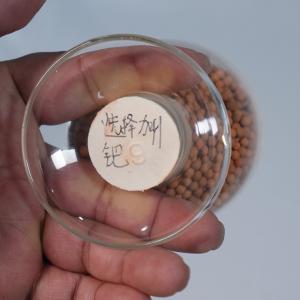

Add to Cart
Description:
The C3 selective hydrogenation catalyst is designed to address the
challenges associated with C3 fractions, which are primarily
sourced from units that utilize diesel, naphtha, or light
hydrocarbons for cracking, as well as from methanol-to-propylene
(MTP) processes and propane dehydrogenation units in refineries.
Notably, C3 fractions produced by refinery units typically lack
acetylene and propylene diene (MAPD), while those from other
sources may contain MAPD at concentrations of 4-6 mol%.
For chemical-grade propylene, the acceptable limit for MAPD is ≤ 15 ppm. Therefore, effective treatment to remove MAPD is essential to meet this standard. Catalytic selective hydrogenation presents a viable solution for this issue. Through the hydrogenation process, hydrogen (H2) reacts with propylene and MAPD, converting them into propylene and significantly reducing the MAPD content to ≤ 15 ppm.
The catalyst not only facilitates the removal of unwanted compounds but also enhances the yield of propylene, making it a crucial component in refining and chemical production processes. Overall, the C3 selective hydrogenation catalyst plays a vital role in improving the purity and yield of propylene, thereby ensuring compliance with industry standards and optimizing production efficiency.
Specifications:
Specification | Details |
Catalyst Composition | Typically contains metals like Pd, Ni, Cu |
Pore Structure | Bimodal |
Specific Surface Area | Typically varies (exact value may vary) |
Small Pore Diameter | Usually in the range of 10-50 nm |
Macro-Pore Diameter | Typically between 80-500 nm |
Hydrogenation Efficiency | Reduces MAPD content to ≤ 15 ppm |
Application Area | C3 fraction purification |
Yield Improvement | Increases propylene yield |
Chemical Purity Requirement | MAPD ≤ 15 ppm for chemical-grade propylene |
Operating Conditions | Varies based on specific process needs |
Applications:
The C3 selective hydrogenation catalyst plays a critical role in
the processing of C3 fractions derived from various sources,
including cracking units that utilize diesel, naphtha, or light
hydrocarbons, as well as from methanol-to-propylene (MTP) and
propane dehydrogenation units in refineries. One of the significant
challenges in handling these C3 fractions is the presence of
acetylene and propylene diene (MAPD), which can adversely affect
the quality of the final product.
Refinery-produced C3 fractions typically do not contain MAPD, while
those from other units may have it in concentrations ranging from
4% to 6%. Given that the acceptable level of MAPD in chemical-grade
propylene is less than or equal to 15 ppm, effective removal of
these compounds is crucial for compliance with industry standards.
The application of catalytic selective hydrogenation is an
efficient method for this purpose. During the hydrogenation
process, hydrogen reacts with propylene and MAPD, transforming them
into propylene and significantly lowering the MAPD concentration to
meet the required specifications. This process not only purifies
the propylene but also enhances its yield, making it advantageous
for industrial applications.
Furthermore, the C3 selective hydrogenation catalyst is essential
in improving the overall quality of propylene used in various
chemical syntheses and manufacturing processes. By ensuring that
the propylene is free from impurities like MAPD, the catalyst
supports the production of high-purity chemicals that are vital for
downstream applications, including the production of plastics,
fibers, and other synthetic materials.
In summary, the C3 selective hydrogenation catalyst is
indispensable in the petrochemical industry. It facilitates the
efficient removal of undesirable compounds, enhances propylene
yield, and ensures that the final product meets stringent quality
standards, ultimately contributing to more sustainable and
efficient production processes.