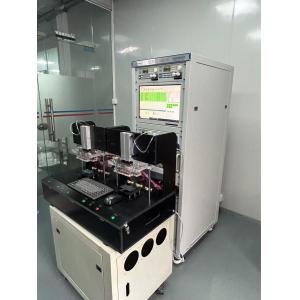

Add to Cart
Test Equipment Comprehensive Tester For Fast Charging Of 2/4/6/8/12/16 Circuits ATE Conventional Power Supply Testing System
Performance Optimization: During the research and development stage of the power supply, the ATE system can assist engineers in quickly and accurately measuring the performance parameters of the power supply and analyzing its performance bottlenecks, thereby facilitating targeted optimization design. For example, if the test reveals that the power supply's conversion efficiency is low, engineers can adjust the circuit topology and select appropriate components to improve the conversion efficiency.
Fault Analysis: When the power supply malfunctions or exhibits abnormal performance, the ATE system can help engineers quickly pinpoint the cause of the fault through detailed test data and analysis tools. This aids in shortening the development cycle, reducing costs, and enhancing the quality and reliability of the power supply.
Compatibility Testing: For power supplies that need to be used in conjunction with a variety of devices, such as adapters and chargers, the ATE system can conduct compatibility tests. It detects the degree of matching between the power supply and different devices and whether there are any compatibility issues, to ensure that the power supply can function normally in practical applications.
Production Line Testing: During the production of the power supply, the ATE system can serve as an automated testing device on the production line, conducting rapid testing and selection of each power supply. This can improve production efficiency, reduce errors and workload of manual testing, and ensure that every power supply leaving the factory meets quality standards.
Quality Traceability: The ATE system can record the test data and results of each power supply, forming a quality traceability system. In case of quality problems, the root cause can be quickly identified by querying the test data, allowing for corresponding corrective measures to be taken. At the same time, it also helps analyze the trend of quality fluctuations during the production process and continuously improve the production process.
Input test | Charge test |
Input voltage ramp | Charge current test |
Input freq. ramp | Full charge testing |
AC cycle drop out | slow charge test |
Input power supply distortion mode | Slow Charge ID setting test |
Input RMS current | Discharge while charge test |
input power | Electricity indication test |
Input power factor | Simulation battery function |
Input peak current test | Wireless charging test |
Output test | Timing / dynamic test |
DC output voltage | Turn ON time |
DC output current | Rise time |
Power up sequence | Fall time |
Power off sequence | Hold-up time |
Tracking | Special test |
Efficiency test | LED lamp voltage and status test |
Overshoot voltage test | LED flashing frequency test |
Peak-Peak noise | Sleep mode test |
Stability test | D + / D-voltage test |
Voltage regulation | MCU communication and calibration tests |
Current regulation | Discharge test |
Mixed effect test | GPIB read/write |
Protection test | USB read/write |
Short circuit test | RS232 read / write |
OV protection | TTL signal control |
UV protection | Relay control |
Charge protection test | Bar code scan |
Discharge protection test | Extended measurement function |
Overcurrent protection test | |
Fast charge test(Applicable to QC2.0, QC3.0 and other fast charge test) |