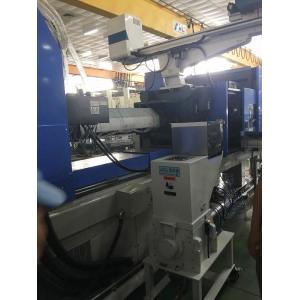

Add to Cart
OG-LS Low-speed Granulator Granulating Machine.pdf...
1. For OG- series granulators, teeth cutter and cutting blades are
integrally fitted in one cutting chamber. Regrinds could be used
with virgin materials.
2. New-type inclined teeth cutter reduces the possibility of stress
concentration, enhance bearing capacity and converts force
direction so that cutter lifespan can be prolonged.
3. The material collector is located outside the cutting chamber to
avoid leakage.
4. Optimum cutting angle makes resistance small and avoid blockage
to improve cutting efficiency.
5. Optimal design can effectively reduce vibration during operation
of granulator.
6. Cutting chamber is made of mirror finished stainless steel,
which is durable and elegant.
7. Low speed granulating ensures well-proportioned granules and low
dust level.
8. Low speed and sound-proof material hopper brings a quiet
operation environment.
9. Easy access to maintenance and cleaning.
10. Small in size with castors for easy moving.
OG series granulators are applied to granulate sprues or few defects. They are always collocated with robots or belt conveyors beside the injection moulding machine. They feature low speed, big driving torque, low noise, few dust and easy operation.
Model | Motor Power | Hopper Size (mm) | Qty. of Staggered Cutter | Qty. of Teeth Cutter | Rotating Speed (rpm) | Max. Capacity (kg/hr) | Dimension L*W*H (mm) | Weight (kg) | |
kw | hp | ||||||||
OG-1217-1LS | 0.75 | 1 | 230*165 | 1 | 2 | 27~35 | 15 | 540*320*880 | 165 |
OG-2326-2LS | 1.5 | 2 | 230*255 | 2 | 3 | 27~35 | 20 | 540*400*900 | 200 |
OG-2626-3LS | 2.2 | 3 | 260*261 | 2 | 3 | 27~35 | 20 | 540*400*900 | 220 |
OG-2636-3LS | 2.2 | 3 | 260*360 | 3 | 4 | 27~35 | 25 | 610*500*920 | 250 |
OG-2636-5LS | 3.75 | 5 | 260*360 | 3 | 4 | 27~35 | 25 | 610*500*920 | 270 |
OG-3136-5LS | 3.75 | 5 | 310*360 | 3 | 4 | 27~35 | 30 | 610*500*920 | 300 |
OG-LS low speed granulators adopt good brand motor with high-torque and low noise level, it is specially applied for grinding small objects like sprues, small defects products to recycle the plastic material. It is always installed beside the injection molding machine to recycle the plastic instantly when the robot pick out the sprues from the injection machine. The materials can be cycled in very short time, it save the cost for storing, transportation and labor cost, compared with the central fast speed granulators.
ORSTE’s large scale Central Material Conveying System and cooling water circulation system including three major systems of centralized raw material drying, water temperature control and metering & mixing, are extensively applied in plastic injection molding industry.
The main products of the company are a series of high-tech products including Desiccant Honeycomb Dehumidifiers, Hopper Dryers, “Three-in-one” Compact Dryers, Auto / Semi-auto Weighing & Packing Machine (for plastic 25kg packages), Auto-loaders, Mold Temperature Controllers, Industrial Chillers, Mixers and Blenders, Masterbatch Dosers, Granulators, and Vibrating Screens.