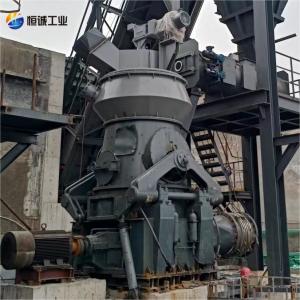

Add to Cart
Limestone Vertical Powder Mill 80t/h High Capacity Vertical Mill Vertical Grinding Equipment Energy Saving Low Consumption
Description
Product Introduction
1, Working principle of vertical mill limestone:
The grinding process of a vertical mill is completed by a set of
grinding devices (i.e. rollers and discs), where the material is
ground into powder between the rollers and discs. The movement of
the grinding device is driven by the rotation of the grinding disc
and the corresponding transmission of the grinding roller. In
addition to the weight of the grinding roller, the grinding
pressure mainly relies on a set of hydraulic devices to pressurize
the material of the grinding disc. After grinding, there is a large
amount of coarse powder in the material. The powder is selected by
a matching powder selection machine, and the powder selection
process is through air flow sorting. During the air flow process,
most of the coarse powder automatically falls onto the grinding
disc and is received for re grinding. The rest is selected as
finished products by the powder selection machine and sent to the
finished product storage warehouse through the dust collection and
transportation system.
2, Main features of the product
1. Efficient and energy-saving:
(1) High grinding efficiency, low energy consumption, compared to
ball mills, energy consumption is 40% -50% lower;
(2) Single machine production capacity is large, and low valley
electricity can be utilized;
(3) Vertical grinding technology and equipment are vigorously
advocated as new energy-saving and consumption reducing
technologies, which are conducive to enhancing the competitive
strength of enterprises in the powder industry in this region and
even nationwide;
2. Easy maintenance and low operating costs:
(1) The grinding roller can be flipped out of the machine using a
hydraulic device, and the replacement of the roller sleeve liner
and the maintenance space of the mill are large, making the
maintenance operation very convenient;
(2) The grinding roller sleeve can be flipped over for use,
extending the service life of wear-resistant materials;
(3) Before starting up, there is no need to place fabric on the
grinding disc, and the mill can be started without load,
eliminating the difficulty of starting up;
(4) Low wear, special materials are used for the grinding rollers
and disc liners, resulting in a long service life;
(5) High degree of automation: The automatic control technology
adopts Siemens series PLC from Germany, equipped with an automatic
control system, which can achieve remote control and is easy to
operate. The workshop can basically achieve unmanned operation,
saving operating costs;
3. Low comprehensive investment cost:
Integrating crushing, drying, grinding, and conveying, the process
flow is simple, the system equipment is few, the structural layout
is compact, and the land area is only 50% of that of a ball mill.
It can be arranged outdoors, with low construction costs, directly
reducing enterprise investment costs.
4. Stable product quality:
(1) The material stays in the grinder for a short period of time,
making it easy to detect the particle size distribution and
composition of the product, and ensuring stable product quality;
(2) The product has uniform particle shape, narrow particle size
distribution, good fluidity, and strong adaptability.
5. High reliability
(1) Adopting a grinding roller limiting device to avoid severe
vibration caused by material breakage during the working time of
the mill;
(2) Adopting a new type of roller sealing device, the sealing is
more reliable and does not require a sealing fan, further reducing
the oxygen content inside the mill and achieving better explosion
suppression performance.
6. Environmental protection:
(1) The entire system of HVM vertical grinding machine has low
vibration and low noise;
(2) The system is sealed as a whole, operates under full negative
pressure, and has no dust leakage, basically achieving a dust-free
workshop.
(3) The ultra-fine limestone vertical grinding machine is a
specialized equipment for desulfurization gypsum, calcite,
limestone, and other fields. It has advantages and characteristics
that cannot be compared to other ordinary rolling mills. It is the
preferred equipment for promoting large-scale non-metallic ore
fields.
Vertical Mill Working Principle:
The main motor drives the grinding disc to rotate through a
reducer, and the material enters the vertical mill main machine
through a screw conveyor. It is then subjected to gravity and falls
to the center of the grinding disc. At the same time, the airflow
generated by the fan enters the main machine through the air inlet.
Under the action of centrifugal force, the material moves uniformly
from the center to the edge of the grinding disc. When passing
through the roller conveyor area on the grinding disc, it is
crushed by the grinding rollers, and large blocks of material are
directly crushed. Fine particles of material are compressed to form
a material layer for inter particle crushing. The crushed material
continues to move towards the edge of the grinding disc until it is
carried away by the strong air flow of the annular guide groove on
the periphery of the grinding disc. Coarse materials fall back into
the grinding disc due to their high gravity and are ground again;
Fine materials enter the powder selection system above the main
machine for classification as the airflow rises. Under the action
of the rotor blades of the classifier, coarser particles are
knocked off by the blades and returned to the grinding disc for
grinding. Qualified fine powder will be carried out of the powder
selection system with negative pressure air flow, enter the dust
removal equipment, and then collected by the powder collector to
form the finished product. In addition, other large particle
materials and debris will fall into the lower chamber of the mill
during grinding, and be scraped into the slag discharge port by the
scraper, effectively ensuring the quality of the finished product.
By adjusting the pressure of the hydraulic system, the grinding
roller pressure can be adjusted to adapt to different hardness raw
materials within a certain range. The rotor speed of the grading
system with multiple grading wheels can be adjusted and controlled,
and various qualified products with different specifications can be
obtained.
Technical Data
Model | HVM1250 | HVM1300 | HVM1500 | HVM1700 | HVM1900 | HVM2400 | HVM2500 | HVM2800 |
Grinding Table Median Diameter(mm) | 1250 | 1300 | 1500 | 1700 | 1900 | 2400 | 2500 | 2800 |
Capacity(t/h) | 6~9 | 9~13 | 15~20 | 24~32 | 26~35 | 36~45 | 45~58 | 56~80 |
Material Moisture | ≤5% | |||||||
Limestone Powder Fineness | 325 mesh (44um) 90% passed | |||||||
Main Motor Power(kw) | 110/132 | 185/200 | 250/280 | 355/400 | 450/500 | 450/500 | 710/800 | 1120/1250 |
Re:The data based on Mohs'hardness 3-4 material
Limestone Bond Index≤13kwh/t
3, In the field of desulfurization gypsum resource treatment, using high-quality and efficient desulfurization gypsum ultrafine
vertical grinding production lines can quickly improve the grinding
efficiency of the entire desulfurization gypsum, helping customers
create large market value. The price of ultra-fine vertical
grinding equipment is adjusted for multiple factors and not
directly controlled by the manufacturer. The price of ultra-fine
vertical grinding equipment is calculated by integrating various
unstable factors such as materials, labor, factory location, and
regional differences.
In general, milling machine manufacturers with real talents and
knowledge not only support online inquiries, but also welcome
customers to conduct on-site inspections of production bases and
milling production lines offline. After all, while online shopping
brings convenience, there are doubts about the reliability of the
grinding machine. Therefore, if a milling machine manufacturer only
supports online consumption, customers may need to improve the
inspection of the actual operation effect of the milling machine
products to prevent purchasing "three no" equipment. Seeing is
believing, and grinding machine manufacturers who support offline
inspections or video viewing have high reliability.
4, Application field
The HVM vertical grinding machine, with its scientific and
reasonable design and unique structural advantages, is widely used
for grinding various types of materials in various industries. The
materials ground range from high humidity to dry, from
exceptionally difficult to easy to grind, and the product fineness
ranges from coarse to fine. The processed powder types are diverse,
involving numerous industries:
① Moisture content of grinding materials: From materials with a
moisture content of 20-30% (such as calcium carbide slag, brown
coal, chalk soil, etc.) to materials with a moisture content less
than 1% (cement clinker, etc.), the materials have strong
adaptability;
② The grindability of grinding materials: from exceptionally
difficult to grind (such as quartz sand, steel slag, slag,
pyroxene, iron ore, etc.) to easily ground (such as gypsum,
calcite, etc.);
③ Grinding product fineness: From 2-5mm (such as new wall material
industry brick raw materials, construction industry sand grinding
shale, etc.) to 15um with a pass rate of 97% (such as papermaking,
chemical industry grinding heavy calcium, etc.), the control of
product fineness is simple and easy;
5, Industry Application of HVM Vertical Grinding Machine
Industries such as building materials, electricity, steel, energy,
heat, chemical, coal chemical, non-ferrous metallurgy, lime kilns,
mineral processing, etc.
The HVM vertical mill can process materials such as ferrite, slag,
slag, cement, diamond, iron ore, chromium ore, manganese ore, gold
ore, copper ore, aluminum ore, lead zinc ore, tantalum niobium ore,
polymetallic ore, nickel ore, bauxite, silicon carbide, titanium
dioxide, talc, bentonite, calcite, kaolin, graphite, mica,
wollastonite, feldspar, dolomite, pyrophyllite, quartz sand,
fluorite, limestone, organic silicon, lithium ash, shale, volcanic
ash, coal, etc.