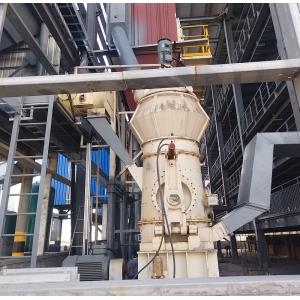

Add to Cart
Coal Mill, Energy-Saving Environmentally Friendly Vertical Mill, Lime Vertical Mill
Product Descripition:
1, What is the process of coal milling?
Coal mills are widely used in coal powder production in fields such
as chemical, metallurgical, and electric power, and are
indispensable and important equipment in coal powder production.
So, how should the process flow be implemented during the operation
of the coal mill? The following text will provide a detailed
introduction.
2, Process flow
1. Coal powder extraction
Firstly, it is necessary to extract coal powder. For the raw coal
before entering the coal mill, it needs to be processed by an
extraction system to extract the coal powder from the coal pile.
Common coal powder extraction methods include vibrating feeders and
spiral feeders, and coal powder extraction requires a uniform and
stable extraction amount.
2. Coal powder preheating
After the coal powder extraction is completed, it enters the
preheating stage, mainly by adding hot air to preheat the coal
powder and achieve a certain drying effect. In addition, the
purpose of this process is to improve the fluidity of coal powder
and facilitate subsequent process operations such as coal powder
conveying and pneumatic conveying.
3. Coal powder drying
After preheating, the coal powder undergoes drying treatment to
evaporate excess moisture from the coal powder, ensuring subsequent
grinding effects. At the same time, it can also improve the
combustibility of the coal powder and reduce the combustion
temperature after drying.
4. Coal powder grinding
The dried coal powder enters the grinding process, and its main
task is to grind the coal powder into fine powder within a certain
particle size range, and achieve uniform and stable particle size
of the coal powder. Common grinding methods include ball mills,
vertical coal mills, etc., which require coal mill equipment to
have the characteristics of high efficiency, energy conservation,
and environmental protection, while also improving production
efficiency and reducing production costs.
5. Coal powder conveying
Finally, the ground coal powder needs to be transported, stored, or
used. Common coal powder conveying methods include pneumatic
conveying, belt conveying, spiral conveying, etc. Coal powder
conveying requires stability and reliability, and maintaining
stable coal powder quality.
Working Principle
The motor drives the grinding disc to rotate through the reducer,
the material falls into the center of the grinding disc from the
feed inlet, and the hot air enters the mill from the air inlet.
Under the action of centrifugal force, the material moves to the
edge of the grinding disc, and is crushed by the grinding roller
when passing through the annular groove on the grinding disc. The
crushed material is carried by the high-speed airflow at the air
ring at the edge of the grinding disc, and the large particles fall
directly on the grinding disc. Re-grinding, when the material in
the airflow passes through the dynamic and static separator, under
the action of the rotating rotor, the coarse powder falls on the
grinding disc for re-grinding, and the qualified fine powder is
ground together with the airflow and collected in the powder
collecting device, which is product. Moisture-containing materials
are dried during contact with hot gas to achieve the required
product moisture.
Parameter Table of Coal Vertical Mill
Specification | HVM1250 | HVM1300 | HVM1500 | HVM1700 | HVM1900 | HVM2200 | HVM2400 | HVM2800 |
Grinding table median diameter(mm) | 1250 | 1300 | 1500 | 1700 | 1900 | 2200 | 2400 | 2800 |
Capacity(t/h) | 10-15 | 10-15 | 14-22 | 20-28 | 26-35 | 35-45 | 45-56 | 70-90 |
Coal Moisture(%) | <15 | |||||||
Coal Power Fineness(%) | R0.08=2-12 | |||||||
Coal Power Moisture(%) | ≤1 | |||||||
Main Motor Power(kw) | 110/132 | 160/185 | 220/250 | 315/355 | 400/450 | 450/500 | 560/630 | 900/1120 |
According to coal coking, it can be divided into anthracite (with a
fixed carbon content of 93-98% and volatile content less than 10%),
lean coal (called semi anthracite, with volatile content between
10% and 20%), bituminous coal (with volatile content greater than
14%), brown coal (with high volatile content and high moisture
content), etc; According to the variety, it can be divided into two
categories: coarse-grained coal powder and fine-grained coal
powder. After being processed by a grinding machine, it can be
applied in the chemical industry, smelting, gas making, glass,
ceramics, ceramic tiles, metallurgical casting industry, etc.
Regarding the coal powder processing technology, the grinding
machine manufacturer will provide you with a detailed explanation:
Phase 1: Crushing and shaping
The coal is crushed by a jaw crusher or a cone crusher, and finally
discharged into a block of material suitable for entering the
grinding machine, with a size of no more than 50mm.
Phase 2: Grinding powder
The small pieces of coal material after crushing only need to meet
the requirements of the vertical coal powder mill before it can be
sent to the silo by the elevator, and then evenly and
quantitatively sent into the coal grinding room for grinding by the
vibrating feeder. The ground material enters the first stage of the
process.
Third stage : Grading and powder collection
The coal material after grinding is classified by a powder
selection machine, and the unqualified powder is classified by the
powder selection machine and returned to the main machine for re
grinding (referring to a vertical coal powder grinding machine).
The fine powder that meets the fineness requirements flows through
the pipeline and enters the dust collector for separation and
collection. The collected finished powder is sent to the finished
material bin by the conveying device through the discharge port.
Stage 4: Packaging and finished products
The coal powder that has reached the finished product will be
uniformly packaged and transported by rotary packaging machines or
automatic loading machines in various industries.
The above is the process of using a vertical coal powder mill to
process coal powder. The quality of coal powder is closely related
to equipment performance, raw material properties, and raw material
composition. The main factors affecting coal powder combustion
include volatile matter, calorific value, fixed carbon, moisture,
sulfur, ash content, and fineness.
Outstanding Advantages
1. Small footprint and low investment cost
2. Adjustable loading force, strong applicability and high milling
efficiency
3. Strong drying ability
4. Product quality is stable easy to maintain