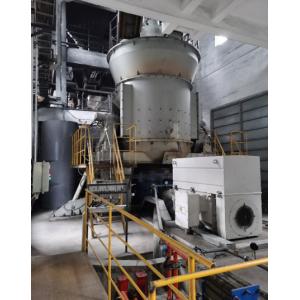

Add to Cart
High Efficiency Limestone Desulfurization Powder Vertical Mill Sodium Bicarbonate Grinding Machine
Limestone Vertical Mill Manufacturer Desulfurization Lime Vertical Mill Large Vertical Mill
Description
The desulfurization limestone vertical mill integrates fine crushing, drying, grinding, powder selection, and transportation, without the need for additional drying, powder selection, and lifting equipment. The dust containing gas from the grinding can be directly collected by a high concentration bag dust collector or electric dust collector, with a compact layout and can be arranged outdoors. The building area is about 70% of the ball milling system, and the building space is about 50-60% of the ball milling system. Therefore, its simple process flow, small footprint and occupied space make the construction cost low.
[Application field]:
grinding of petroleum coke, nonflammable and explosive materials with humidity less than 6% and Mohs hardness below 7 in power plants, building materials, chemicals, metallurgy, coatings, paper making, rubber, medicine, food and other fields.
[Applicable materials]:
limestone, calcite, calcite, bauxite, kaolin, fluorite, talc, water slag, lime calcium powder, wollastonite, gypsum, limestone, phosphate rock, marble, potash feldspar, quartz sand, bentonite, manganese ore and other materials with hardness below Mohs 7.
Technical Data
Model | HVM1250 | HVM1300 | HVM1500 | HVM1700 | HVM1900 | HVM2400 | HVM2500 | HVM2800 |
Grinding Table Median Diameter(mm) | 1250 | 1300 | 1500 | 1700 | 1900 | 2400 | 2500 | 2800 |
Capacity(t/h) | 6~9 | 9~13 | 15~20 | 24~32 | 26~35 | 36~45 | 45~58 | 56~80 |
Material Moisture | ≤5% | |||||||
Limestone Powder Fineness | 325 mesh (44um) 90% passed | |||||||
Main Motor Power(kw) | 110/132 | 185/200 | 250/280 | 355/400 | 450/500 | 450/500 | 710/800 | 1120/1250 |
Re:The data based on Mohs'hardness 3-4 material
Limestone Bond Index≤13kwh/t
Working principle
The electric motor drives the grinding disc to rotate through a reducer, and the material falls into the center of the grinding disc from the feeding port. At the same time, hot air enters the grinding chamber from the air inlet. Under the action of centrifugal force, the material moves towards the edge of the grinding disc and is crushed by the grinding roller when passing through the circular groove on the grinding disc. The crushed material is carried up by the high-speed airflow at the edge of the grinding disc, and large particles directly fall onto the grinding disc for re grinding. When the material in the airflow passes through the dynamic and static separator, under the action of the rotating rotor, the coarse powder falls onto the grinding disc for re grinding, and qualified fine powder is discharged with the airflow, Collect in the powder collection device, which is the product. Materials containing water are dried in the Contact process with hot gas to meet the required product moisture.
Performance advantages:
1. Efficient and energy-saving:
(1) High grinding efficiency and low energy consumption, compared
to ball mills, the energy consumption is 40% -50% lower;
(2) Large single machine production capacity, capable of utilizing
low valley electricity;
(3) Vertical grinding technology and equipment are vigorously
advocated new technologies for energy conservation and consumption
reduction, which are conducive to enhancing the competitive
strength of enterprises in the powder industry in this region and
even across the country;
2. Easy maintenance and low operating costs:
(1) The grinding roller can be turned out of the machine using a
hydraulic device, and the replacement of the roller sleeve lining
plate and the maintenance space of the mill are large, making the
maintenance operation very convenient;
(2) The grinding roller sleeve can be used upside down, extending
the service life of wear-resistant materials;
(3) Before starting the machine, there is no need to apply fabric
to the grinding disc, and the mill can be started without load,
eliminating the difficulty of starting the machine;
(4) Low wear, special materials are used for the grinding roller
and disc lining plate, resulting in a long service life;
(5) High degree of automation: The automatic control technology
adopts the Siemens series PLC from Germany, equipped with an
automatic control system, which can achieve remote control and easy
operation. The workshop can basically achieve unmanned operation,
saving operating costs;
3. Low comprehensive investment cost:
Integrating crushing, drying, grinding, and conveying, the process
flow is simple, the system equipment is few, the structural layout
is compact, and the floor area is only 50% of that of the ball
mill. It can be arranged outdoors, with low construction costs,
directly reducing the investment cost of the enterprise.
4. Stable product quality:
(1) The material stays in the mill for a short time, which makes it
easy to detect the particle size distribution and composition of
the product, and the product quality is stable;
(2) The product has uniform particle shape, narrow particle size
distribution, good fluidity and strong adaptability.
5. High reliability
(1) Adopting a grinding roller limit device to avoid severe
vibration caused by material breakage during the working time of
the mill;
(2) Adopting a new type of roller sealing device, the sealing is
more reliable, and there is no need for a sealing fan, further
reducing the oxygen content in the mill and achieving better
explosion suppression performance.
6. Environmental protection:
(1) The entire system of HVM vertical grinding machine has low
vibration and low noise;
(2) The system is sealed as a whole, operates under full negative
pressure, and there is no dust leakage, basically achieving a
dust-free workshop.