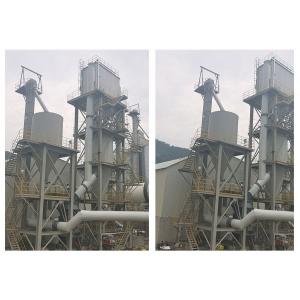

Add to Cart
High Capacity Vertical Mill Prices / Vertical Roller Grinding Mill
Coal Pulverizing Production Line
Product Introduction
HVM vertical mills are also commonly called roller mills, medium-speed mills, etc. in different industries. This model has the characteristics of integrating crushing, grinding, drying, and grading. It can be used for various types of moisture, properties and hardness. It is the ideal equipment for the grinding industry at present.
The vertical mill is mainly composed of base, casing, column, separator (powder separator), reducer, grinding device (grinding disc and grinding roller), rocker arm device, hydraulic loading device, sealing pipeline system, slag discharge device, Operation platform, etc. The supporting equipment includes thin oil lubrication station, hydraulic oil station, dry oil station, main motor, electrical control cabinet, etc.
Vertical mill is an honorary product launched by our company to solve the technical problems of low output and high energy consumption of raw material vertical mill in the production process of cement process. Vertical mill is a grinding and drying equipment with mature technology and superior performance. It is widely used in cement chemical industry, coal, electric power and other departments. It has many advantages, such as drying, grinding and powder selection. It has become a mainstream product in cement grinding industry.
【Working Principle】
The motor drives the grinding disc to rotate through the reducer, the material falls into the center of the grinding disc from the feed inlet, and the hot air enters the mill from the air inlet. Under the action of centrifugal force, the material moves to the edge of the grinding disc, and is crushed by the grinding roller when passing through the annular groove on the grinding disc. The crushed material is carried by the high-speed airflow at the air ring at the edge of the grinding disc, and the large particles fall directly on the grinding disc. Re-grinding, when the material in the airflow passes through the dynamic and static separator, under the action of the rotating rotor, the coarse powder falls on the grinding disc for re-grinding, and the qualified fine powder is ground together with the airflow and collected in the powder collecting device, which is product. Moisture-containing materials are dried during contact with hot gas to achieve the required product moisture.
Technical DATA
Specification | HVM1250 | HVM1300 | HVM1500 | HVM1700 | HVM1900 | HVM2200 | HVM2400 | HVM2800 |
Grinding table median diameter(mm) | 1250 | 1300 | 1500 | 1700 | 1900 | 2200 | 2400 | 2800 |
Capacity(t/h) | 10-15 | 10-15 | 14-22 | 20-28 | 26-35 | 35-45 | 45-56 | 70-90 |
Coal Moisture(%) | <15 | |||||||
Coal Power Fineness(%) | R0.08=2-12 | |||||||
Coal Power Moisture(%) | ≤1 | |||||||
Main Motor Power(kw) | 110/132 | 160/185 | 220/250 | 315/355 | 400/450 | 450/500 | 560/630 | 900/1120 |
Low Operation Cost
(1) Low energy consumption: the grinding roller is used to directly roll and grind the materials on the grinding plate, which has low energy consumption and saves 40% ~ 50% energy consumption compared with the ball milling system.
(2) Less wear: because the grinding roller is not in direct contact with the grinding disc during work, and the grinding roller and lining plate are made of high-quality materials, it has long service life and less wear.
High Grinding Efficiency
The grinding force can be increased by hydraulic pressurization,
which can increase the output and improve the grinding efficiency;
At the same time, it is also equipped with a limiter device, which
only grinds the materials to prevent the accidental contact of the
grinding roller and grinding ring from causing the vibration and
even wear of the equipment.
Convenient Maintenance
By overhauling the oil cylinder, turning over the boom and replacing the roll sleeve and lining plate, it is convenient and fast to reduce the shutdown loss and save the labor cost.