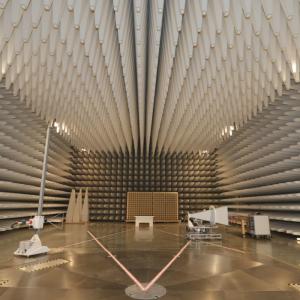

Add to Cart
GLOBAL UNITED TECHNOLOGY SERVICER CO., LTD
GTS professional auto parts auto brake testing certification
third-party authoritative laboratory
Automotive materials and parts
Provide various kinds of automotive materials and parts inspection
certification
Automobile is an electromechanical hybrid system composed of tens
of thousands of parts. Auto parts inspection can help auto
manufacturers and parts manufacturers get detailed reports on the
quality of parts, so as to improve the performance of parts.Testing
covers environmental reliability testing of auto parts,Electrical
performance test, functional test, EMC test,Material testing, green
environmental testing and chemical compliance services.
Product range
Auto parts are mainly composed of eight parts: auto steering parts,
auto walking parts, auto electrical instrument parts, auto lamps,
auto modification parts, engine parts, transmission parts, and
brake parts.
1. Automotive steering components: kingpin, steering machine,
steering knuckle, ball pin, etc.
2. Car walking parts: rear axle, air suspension system, balance
block, steel plate, etc.;
3. Automotive electrical instrumentation components: sensors,
automotive lamps, spark plugs, batteries, etc.
4. Automobile lamps: decorative lights, fog lights, ceiling lights,
headlights, searchlights, etc.
5. Auto modification parts: tire pump, car top box, car top rack,
electric winch, etc.
6. Engine parts: engine, engine assembly, throttle body, cylinder
block, tension wheel, etc.
7. Transmission system parts: clutch, transmission, variable speed
shift lever assembly, reducer, magnetic materials, etc.
8. Brake parts: brake master pump, brake sub pump, brake assembly,
brake pedal assembly, compressor, brake disc, brake drum, etc.
Auto parts testing projects are mainly composed of metal parts
testing projects and polymer parts testing projects.
Main test items of auto metal parts are:
1. Mechanical performance test: tensile test, bending test,
hardness test, impact test, etc.;
2. Composition analysis: qualitative and quantitative composition
analysis, trace element analysis, etc.;
3. Structure analysis: metallographic analysis, nondestructive
testing, coating analysis, etc.;
4. Dimension measurement: coordinate measurement, projector
measurement, precision caliper measurement, etc.
The main testing items of automotive polymer components include:
1. Physical performance test: tensile test (including normal
temperature and high and low temperature), bending test (including
normal temperature and high and low temperature), impact test
(including normal temperature and high and low temperature),
hardness, fog, tearing strength, etc.;
2. Thermal performance test: glass transition temperature, melting
index, Veka temperature softening point, low temperature
embrittlement temperature, melting point, thermal expansion
coefficient, thermal conductivity coefficient, etc.;
3 rubber and plastic electrical performance test: surface
resistance, dielectric constant, dielectric loss, dielectric
strength, volume resistivity, voltage resistance, breakdown
voltage, etc.;
4. Combustion performance test: vertical combustion test,
horizontal combustion test, 45° Angle combustion test, FFVSS 302,
ISO 3975 and other standards;
5. Qualitative analysis of material composition: Fourier infrared
spectroscopy, etc.
Routine test items
1, safety project:
Input current test, label to wipe test, energy level test, SELV
test, current limiting circuit testing (LCC), limited power test
(LPS), grounding continuity test, temperature and humidity (tide)
test, drop, impact and other mechanical stress tests, the ball
pressure test and normal temperature test, contact voltage,
electric current test, insulation test voltage, abnormal test, yuan
A fault testing, etc.
2, the EMC test project:
Conduction, radiation, harmonic, voltage fluctuation and flicker,
electrostatic, RS, EFT, surge, CS, power frequency magnetic field,
such as voltage sag.
Environmental reliability Testing
High and low temperature resistance test, heat and humidity
resistance, high and low temperature impact, high and low
temperature alternating, mechanical vibration, mechanical impact,
low pressure (vacuum) test, IP grade, dustproof water release test,
gas corrosion (single/multiple), salt spray corrosion test
(neutral, acid, compound), etc.
Class specific tests
Battery charging and discharging test, impact test, impact test,
drop test, ROhs testing, REACH, halogen detection, temperature and
humidity environment test, failure analysis, components selection,
pressure test, light aging test, sand and dust test, get wet in the
rain test, vibration test, high speed test, mechanical shock test,
biological environment test, salt spray test and reliable
integrated environment Sex test, simulated packaging and
transportation test, gas corrosion test, slice test, etc.
Energy efficiency test
Energy saving testing, energy efficiency testing
Electrical performance testing
Operating voltage, operating current, speed range, power,
conductivity, dielectric constant, dielectric loss, field strength
(breakdown voltage), etc
Automobile brake performance inspection
In order to meet the braking requirements of the driving state,
improve the braking stability, reduce the rear axle wheel sideslip
and the car tail swing during braking, the front axle braking force
generally accounts for about 50 ~ 70%, and the rear axle braking
force design is relatively less. In addition also make full use of
inertia force when the car braking, leading to the vehicle center
of gravity forward axle weight changes, the characteristics of the
front axle braking force can be up to 140% of the static axle load,
the braking characteristics reflected only when road test, on the
roller reaction type test bench, due to the limitation of device
structure and test method, the front axle maximum braking force
cannot be measured.
Brake inspection standard
1. Braking force requirements: the ratio of front axle braking
force and front axle load ≥ 60%; The ratio of total braking force
and vehicle weight, no load ≥ 60%, full load ≥ 50%; The ratio of
rear axle braking force to rear axle load of passenger cars and
trucks with a total mass of less than 3500kg is ≥ 20%.
2. Braking balance requirements: in the whole process of braking
force growth measured at the same time in the left and right wheel
braking force difference of the maximum, and the whole process
measured in the shaft left and right wheel braking force of the
largest ratio, the front shaft should not be more than 20%; For the
rear shaft (and other shafts) in the shaft brake force is not less
than 60% of the shaft load, should not be greater than 24%; When
THE BRAKING FORCE OF THE REAR SHAFT (and OTHER SHAFTS) is less than
60% OF THE axle load, THE MAXIMUM difference OF THE braking force
between the LEFT AND RIGHT wheels measured simultaneously during
the whole process of braking force growth should not be greater
than 8% of the axle load.
3. Coordination time requirements: GB7258-2004 provisions: the use
of hydraulic brake system of the vehicle shall not be greater than
0.35S; For the vehicle using pneumatic brake system shall not be
greater than 0.60s; The braking coordination time of automobile
train, articulated bus and articulated trolleybus should not be
more than 0.80s. GB18565 provisions: the use of hydraulic braking
system of the vehicle shall not be greater than 0.35S; Not more
than 0.56s for the vehicle with pneumatic brake system.
4. Resistance requirement: The resistance of each wheel of the
vehicle shall not be greater than 5% of the axle load when the
braking force is tested.
5. Parking braking force requirements: the total parking braking
force should not be less than 20% of the vehicle weight in the test
state; This value is 15% for vehicles whose total mass is less than
1.2 times the mass of the assembly.
6. Brake complete release time requirements: vehicle brake complete
release time (from the release of the brake pedal to the time
required for brake elimination) should not be greater than 0.80s.
2. Certification services
CCC, CQC, CQM, CB, CE, GS, EMF, ErP, UL, ETL, FCC, CEC, DOE, SAA,
RCM
We are committed to the testing and international certification of
information technology, audio and video, home appliances, lamps,
wireless communications, power tools and machinery, electronic
instruments, medical instruments and other types of products. We
have obtained the qualification recognition of UL, Intertek, CSA,
MET, TUV-RH, TUV-SUD, SGS, NEMKO, FCC, IC and many other
international certification bodies. We can provide customers with
professional and authoritative one-stop testing and certification
services.
The test report issued by Global Zhongyi has legal effect and can
be used in scenarios such as the entry of supermarkets, product
appeals, anti-malicious rights protection, and auctions (appeals
and auctions must meet Party A's testing requirements).