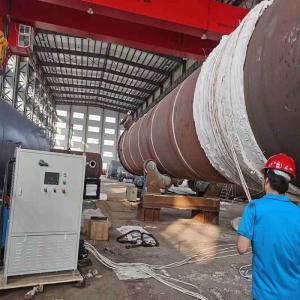

Add to Cart
Manfacturer supply Electromagnetic induction heating equipment for pre-heating before welding pipes:
The equipment requires a solution based on the workpiece to be machined provided by the customer.
Name | Full Digital Air Cooled Induction Heating Machine | ||||||
Work Mode | Manual Mode and Temperature Mode | ||||||
Alarm System | Over Current, Over Voltage, Fail Phase, Driver Board Over Current , Loading abnormal, out off control protection. | ||||||
Special Function | Using DSP and ARM full digital control circuit, the equipment has rich communication interface, support optical fiber, Ethernet, RS485/233, Profibus, CAN and other industrial buses, CAN achieve remote control | ||||||
Model | DIH-60KW | HID-120KW | DIH-200KW | DIH-300KW | |||
Output Power | 60KW | 120KW | 200KW | 300KW | |||
Frequency | 0.5-10khz | 0.5-10KHZ | 0.5-10KHZ | 0.5-10KHZ | |||
Work Voltage | 380V/415v/440v/480v*3phase 50-60hz | ||||||
Power Factor | 0.93 | ||||||
Min Circuit Breaker | 3P-125 | 3P-160 | 3P-200 | 3P-600 | |||
Cooling Way | Air Cooled Type |
1.Advanced technology: digital intelligent power supply using DSP processor control, the
use of digital control technology, the control process of the
system, data operation, parameter storage, etc. all in the form of
digital processing, environmental changes such as temperature
changes will not affect the details of the internal processing and
results, all digital intelligent power supply using new
international technology, many features are not available in the
analogue power supply (for example: frequency variable load
adaptive (e.g. variable frequency load adaption, energy monitoring
system, fault self-diagnosis, intelligent protection system, good
anti-voltage fluctuation performance, high power control accuracy
(+0.5%), 0.1s fast start, 99% start-up success rate, etc.).
2. Touch screen display: the working status and working parameters of the equipment can be
displayed intuitively on the touch screen, display parameters
include: working frequency, oscillation current, power parameters,
etc.
3. Intelligent protection system power supply: If it suddenly encounters bad working conditions during normal
operation, it will automatically lock up the fault alarm, and then
judge various signals and issue fault alarm respectively. Such as:
IGBT extreme speed protection, diode special protection,
over-voltage, over-current, phase failure, water shortage, water
temperature and other kinds of protection to ensure reliable and
durable equipment.
4. Fault self-diagnosis and online external management: when the alarm occurs due to misoperation or special working
conditions, the touch screen will display the fault content, and
the solution of the corresponding fault can be inquired by clicking
on the help of the corresponding fault. More than 90% of common
faults can be quickly dealt with by the operator, which greatly
improves production efficiency and reduces the reliance on the
operator's technical level.
5. Full digital control system: traditional analogue power supply, using analogue devices to
control parameters determined by potentiometers and other analogue
devices, these devices are affected by the environment is more
obvious, such as temperature changes will cause changes in
parameters, resulting in the equipment in the temperature change,
such as winter and summer, day and night and other different
temperature environment, without any adjustment changes in the case
of some differences in output power. Our fully digital intelligent
power supply is controlled by DSP processors, using digital control
technology, the control process of the system, data operation,
parameter storage, etc. are all processed in digital form,
environmental changes such as temperature changes will not affect
the internal processing and results of the system, the control and
output of the system is extremely stable, and the control
parameters are cured in digital form in the program, compared to
the analogue control system, the Compared to analogue control
systems, fully digital power supplies have a higher degree of
stability.
6. Communication function: RS485/232 interface is reserved for exchanging data with external
controllers (industrial computer, industrial touch screen, laptop,
etc.) or central control room.
7. Use of internationally renowned brand components: All key components on the equipment are imported, and some of them
are made of domestic first-tier brands, which makes the operation
more stable and reliable. The IGBT of Germany Infineon is used for
the inverter, and the DSP digital processor of the United States TI
is used for the core control device.