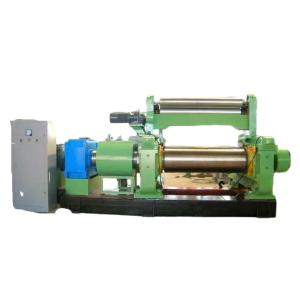

Add to Cart
Energy-saving XK-450 Open Mixing Mill ,The Ultimate Mixing Solution For Rubber And Plastic Processing
Open mill: a powerful assistant for rubber and plastic processing
Open mill, also known as rubber mixing mill, open mill or mixing
mill, is an indispensable equipment in rubber and plastic
processing. Its main working parts are two hollow rollers rotating
in opposite directions, one is fixed and the other can be moved
forward and backward manually or electrically to adjust the roller
distance to meet different operating requirements.
1.Working principle:
The raw rubber or rubber material is rolled into the gap between
the two rollers under the rotation of the rollers and is subjected
to strong shearing action, thereby achieving the purpose of
plasticizing or mixing. This equipment is also widely used in
plastic processing and other fields.
2.Application of open mill:
In plastic product factories, open mills are usually called
two-roll mills. It is one of the earliest mixing equipment used in
the production of plastic products. On the calender production
line, the open mill is responsible for mixing and plasticizing the
uniformly mixed raw materials to provide uniform molten material
for the calender.
3.Structure and characteristics of open mill:
Simple structure, easy to manufacture and maintain, and easy to
master operation. Nevertheless, the open mill also has its
limitations, such as the large physical exertion of workers when
operating it, and the need to manually turn the mixed material
under high temperature environment, which will affect the mixing
quality of the raw materials.
4.The versatility of the open mill:
The open mill can not only be used for mixing rubber and plastic,
but also for recycling waste plastic film for re-refining. In the
floor leather production line, the open mill can provide a uniform
base coating for the cloth leather.
In general, the open mill is widely used in plastic product enterprises. Although there are some shortcomings, it is still an indispensable part of the production process.
Type | XK-250 | XK-300 | XK-360 | XK-400 | XK-450 | XK-560 | XK-550 | XK-610 |
Rolls Working Diameter(mm) | 250 | 300 | 360 | 400 | 450 | 560 | 550 | 610 |
Rolls Working Length(mm) | 620 | 750 | 900 | 1000 | 1200 | 1530 | 1530 | 1930 |
Working Linear Speed of Front Roll (m/min) | 15.1 | 15.1 | 16.25 | 18.65 | 24.5 | 27.7 | 27.7 | 30.5 |
Max Gap (mm) | 10 | 10 | 10 | 10 | 15 | 15 | 15 | 15 |
Capacity Per.Batch (kg) | 10-15 | 15-20 | 20-25 | 18-35 | 25-50 | 50-65 | 50-65 | 140 |
Driving Motor Power (KW) | 18.5 | 22 | 30 | 37 | 55 | 95 | 95 | 160 |
Overall Dimension(L*W*H) (mm) | 3400*1350*1500 | 3580*1550*1695 | 3940*1780*1740 | 4250*1850*1770 | 5200*2380*1970 | 6120*2500*2100 | 6120*2500*2100 | 6475*3146*2035 |
Weight (KG) | 3500 | 5200 | 5670 | 7600 | 13000 | 22000 | 22000 | 44000 |