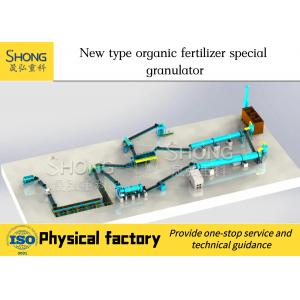

Add to Cart
Environment Protection Fertilizer Pellet Machine Organic Fertilizer Granule Production Line
Raw material of Environment Protection Fertilizer Pellet Machine
Organic Fertilizer Granule Production Line
1. Agricultural waste: straw, dregs of beans, cotton dregs, rice
bran, etc.
2. Animal manure: mixture of poultry litter and animal waste, such
as the wastes of slaughterhouse, fish market, urine and dung of
cattle,
pigs, sheep, chicken, ducks, geese, goat, etc.
3. Industrial waste: wine lees, vinegar residue, manioc waste,
sugar scum, furfural residue, etc.
4. Home scrap: food waste, the roots and leaves of vegetables, etc.
5. Sludge: the sludge of the river, sewer, etc.
Introduction of Environment Protection Fertilizer Pellet Machine
Organic Fertilizer Granule Production Line
The bio-organic fertilizer production plant is commonly used to
process different fermented organic substance into bio-organic
fertilizer. It adopts one-step molding technology. Animal manure
and agricultural waste are recycled as the main raw materials, thus
manure or dung waste is not only creating economic benefits for the
enterprise, but also making a great contribution to environmental
projects for mankind.
Features of Environment Protection Fertilizer Pellet Machine
Organic Fertilizer Granule Production Line
1. The line takes animal manure and agricultural waste as its main
material, not only turns the waste into valuable things, but also
protects
the environment.
2. The whole fertilizer production process is centralized
controlled, so this series of fertilizer machines are highly
automatic and easy to
operate.
3. Both batching system and packing system are controlled by the
computer, thus ensuring the precision of material batching and
fertilizer
packing.
4. High-quality, stable performance, compact process layout,
advanced technology, and convenient maintenance.
The process of Environment Protection Fertilizer Pellet Machine
Organic Fertilizer Granule Production Line
Bio-organic Fertilizer Production plant is a complete set of
equipment from raw materials collection to the organic fertilizer
packing.
The whole organic fertilizer production line include the following
machines:Raw material Fermentation→ fertilizer crushing machine→
fertilizer mixing machine → rotary drum granulator → rotary drum
drying machine → rotary drum cooling machine → rotary drum coating
machine → rotary screening machine → packaging machine → spraying
granulating system→ belt conveyor → and other accessories.
1.Organic materials fermentation process plays the preliminary but
indispensable role in the whole production line. Two main types of
compost turner are widely used to turn and mix the compost and
accelerate the fermentation speed: Self-propelled compost turner
and hydraulic compostturner.
2.Crushing Process: The compost lump materials should be ground
before the granulating process. But we can leave out crushing
process when the compost material is fine enough. Vertical chain
crusher and double-shaft horizontal crusher, two types of crushing
machine can be used to crush lump compost fertilizer raw materials.
3.Mixing Process, two types of mixing machine are applied to mix
raw materials in the fertilizer production line: horizontal mixer
and vertical mixer.
4.Drying process. When granulating, the moisture of fertilizer raw
materials should be less than 25%, so we should dry the raw
materials if the moisture is more than 25%. Rotary drum drying
machine is mainly used for drying the fertilizer with a certain
degree of humidity and particle size.
5.Granulator Process. Granulating process is the core part in this
production line, so we choose the suitable model of fertilizer
granulator according to customers detailed requirements.
Optional granulator equipment: organic fertilizer combination
granulator, organic fertilizer special granulator, pair roll
extrusion granulator, disc granulator, flat film granulator, bio
organic fertilizer spherical granulator, Drum granulator, round
tossing machine, etc.; Typical application materials: chicken
manure, cow dung, kaolin, etc.
Organic manure, animal manure, manure, manure, composted manure,
green manure, sea manure, cake manure, peat, microbes and other
organic manure fermented fertilizer granules, the particles are
irregular spherical. The granulation rate of Huaqiang Organic
Fertilizer Granulator is over 95%, which is suitable for a variety
of different formulas. The compressive strength of organic
fertilizer is higher than that of disc and drum granulator, and the
particle size is uniform. It is suitable for direct granulation
after fermentation, saving drying process and reducing
manufacturing cost.
6.Rotary Drum Cooling Machine is used for cooling fertilizer to
make fertilizer particles stronger.
7.Screening process:Rotary drum screening machine is used to
separate the granules from the large particles which need to be
returned for the second crushing and granulating. Rotary drum
coating machine is used to coat the fertilizer and prevent the
fertilizer from sticking together.
8.The last process is packaging process. Fertilizer packaging
machine can package bags quantitatively and automatically.Including
electronic quantitative packaging scale, silo, automatic sewing
machine, etc. It also need some auxiliary equipment for connection
such as belt conveyor, bucket elevator, etc.
Our Services
1.Pre-sale services:
1) Selecting equipment type;
2) Designing and fabricating the products in accordance with the
special requirements of the clients;
3) Training technical personnel for our clients;
4) Providing construction and technology consultations or working
out proper construction schemes for those new, special or difficult
projects.
2.Services provided during the sale:
Respect our clients; present the clients with ease, relaxation and
a surprise; devote ourselves to improve the total value of our
clients.
1) Checking products acceptance ahead of delivery;
2) Introducing the service system to our clients.
3. After-sale services:
Improve the added value of our products, and let the clients free
from the using troubles:
1) Assisting the clients preparing for the first construction
scheme;
2) Installing and testing the equipments;
3) Training the first-line operators on site;
4) Examining the equipment regularly;
5) Taking the initiatives to eliminate the failure(s) rapidly at
site;