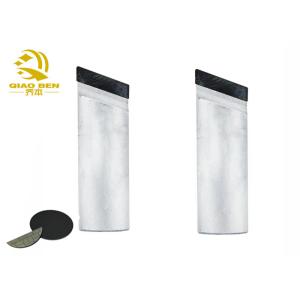

Add to Cart
overview
Polycrystalline Diamond PCD Insert:
PCD (Polycrystalline Diamond) is a synthetic diamond product that is produced by sintering together selected diamond particles with a metal matrix, using sophisticated technology. The diamond and matrix, when sintered together under high temperatures and pressures, creates a PCD tool blank that is high in uniform hardness and is abrasive resistant in all directions. PCD Inserts is made of PCD tips( cutting from PCD blank) and a carbide substrate.
Diamond tool has the characteristics of high hardness, high compressive strength, good thermal conductivity and wear resistance, which can obtain high machining accuracy and processing efficiency in high-speed cutting. The above characteristics of the diamond tool are determined by the crystal state of the diamond. In diamond crystals, the four valence electrons of carbon atoms are bonded by tetrahedral structure, and each carbon atom forms a covalent bond with four adjacent atoms, thus forming a diamond structure, which has a strong binding force and directivity, so that diamond has extremely high hardness. Because the structure of polycrystalline diamond (PCD) is a fine crystalline diamond sintered body with different orientation, the hardness and wear resistance of PCD are still lower than that of single crystalline diamond although the binder is added. However, because the PCD sintered body is isotropic, it is not easy to crack along a single cleavage plane.
The hardness of cubic boron nitride (CBN) is second only to PCD and single crystal diamond. It can maintain the hardness of cemented carbide at 25 ℃ at 1000 ℃. The high strength of CBN comes from its intergranular bond. With the hardness alloy matrix with good hardness and toughness, the tool made of it can bear great cutting force when deep cutting high hardness and toughness materials, and the intergranular bond can also provide high impact strength, which is very necessary when cutting continuous and discontinuous sections.
1. Look at the processing process: if the processing process,
continuous regular sparks, indicating that the tool has been worn,
according to the average life of the tool
Change knives in time.
2. Look at the color of the iron filings: the color of the iron
filings changes, indicating that the processing temperature has
changed, and this time the tool has begun to wear.
3 Look at the shape of the iron filings: zigzag on both sides of
the iron, abnormal curling of the iron filings, and the iron
filings become finer, which are all tools
The judgment basis of damage.
4. Look at the surface brightness change of the workpiece: the
brightness continuously reduces the tool has been worn.
5 Processing vibration sound changes: tool wear will cut the
resistance is too large, pay attention to avoid "knife", resulting
in workpiece scrap
6. Observe the change of machine load data: If there is a
significant incremental change, it indicates that the tool has been
worn.
7. Observe the burr change on the edge of the workpiece: when the
tool is cut out, the workpiece has a serious burr and the phase
roughness decreases.
8. Observe the size change of the workpiece: obvious phenomena such
as the size change of the workpiece are also the criteria for tool
wear.
9. Tool life table (based on the number of processed workpieces):
some high-end equipment manufacturing or single product mass
production enterprises use it to guide production, this method is
suitable for processing expensive aerospace, steam turbines,
automotive key components such as engines and other production
enterprises.
The choice of tool material has great influence on tool life, machining efficiency, machining quality and machining cost. Tool cutting to withstand high pressure, high temperature, friction, impact and vibration and other effects. Therefore, the tool material should have the following basic properties:
(1) Hardness and wear resistance. The hardness of the tool material
must be higher than that of the workpiece material, and it is
generally required to be above 60HRC. The higher the hardness of
the tool material, the better the wear resistance.
(2) Strength and toughness. The tool material should have high
strength and toughness in order to withstand the cutting force,
impact and vibration, to prevent the brittle fracture and blade
collapse of the tool.
(3) Heat resistance. The tool material has good heat resistance,
can withstand high cutting temperature, and has good oxidation
resistance.
(4) Process performance and economy. Tool material should have good
forging performance, heat treatment performance, welding
performance; Grinding processing performance, and the pursuit of
high performance-price ratio.
Application scope of natural diamond milling cutter: hardware
parts; Auto parts; Surface treatment; Craft products; Fine carving;
Copper batch flower; Mobile phone metal keys; Mobile phone case;
Digital shell; Metal highlight batch flower; Watch surface, word
nail; The case reflects the knife; Nameplate, sign highlight batch
flower; Car CD pattern; Car colorful pattern; Car sun pattern;
Aluminum products highlight; Electrical shell batch flower;
Electrical panel; Vehicle panel; Computer peripherals; Transparent
computer case; Acrylic polishing; Compression (plexiglass)
highlight (polishing) chamfer; A lens; Windows; Motor rectifier
fine car, etc. Mainly used for all kinds of metals, gold, silver,
copper, aluminum alloy, zinc alloy and non-metallic materials,
acrylic, PVC, PC, plastic and other materials of high light
chamfering and straight edge mark light cutting, cutting surface
bright mirror highlight effect, long service life. According to the
requirements of customized tool tip diamond width, Angle, material,
tool bar size. R Angle arc can be controlled in 0.02-0.05,
chamfering knife commonly used specifications in 45°, 75°, 78°,
diamond width is 3.0* 3.0mm.
Processing features: strong stability, specular highlight, smooth
chip, reduce cutting resistance, improve processing efficiency and
tool life.
MCD Recommended Cutting Condition | |||
Work piece | Cutting Speed | Depth of Cut | Feed Rate |
(m/min) | (mm) | (mm/rev) | |
Aluminum(5~8% SI ) | 350~1600 | 0.05~2.50 | 0.10~0.40 |
Aluminum(8~12% SI ) | 350~1300 | 0.05~2.50 | 0.10~0.40 |
Aluminum(14~18% SI ) | 160~800 | 0.05~2.50 | 0.05~0.25 |
Copper | 350~1000 | 0.15~2.50 | 0.05~0.20 |
Sintered Carbid | 15~25 | 0.05~0.60 | 0.10~0.20 |
Glass Fiber | 100~800 | 0.15~0.50 | 0.03~0.25 |
Carbon | 160~700 | 0.15~2.50 | 0.15~0.40 |
High Aluminum | 70~250 | 0.05~1.50 | 0.03~0.15 |
Ceramics | |||
Wood | 1000-2500 | 0.2~5.0 | 010~0.50 |
Grade | Work-piece material | Hardness | V(m/min) | F(mm/rev) | Ap(mm) |
CBN | Gray cast iron | HB170-300 | 500-1500 | 0.1-0.4 | 0.1-1.5 |
Nodular cast iron | HB240-300 | 200-400 | 0.1-0.4 | 0.1-0.5 | |
Alloyed cast iron | HB240-300 | 150-300 | 0.05-0.4 | 0.1-0.5 | |
Fe-based P/M | HRC45-50 | 50-150 | 0.05-0.4 | 0.05-0.5 | |
Hardened steels | HRC55-65 | 80-200 | 0.05-0.2 | 0.05-0.2 | |
Heat-resistant alloys | 50-200 | 0.05-0.2 | 0.05-0.2 | ||
PCD | AI and AI alloys | 200-3000 | 0.05-0.5 | 0.05-1.0 | |
Non-mentals Cemented | 100-500 | 0.05-0.5 | 0.05-1.0 | ||
Carbide | 20-30 | 0.05-0.2 | 0.05-0.2 |
Product Name | PCD/CBN/MCD/ND Inserts High Quality Diamond Inserts |
Suitable Material | Gold/Silve/Aluminum/Brass/Acrylic/Plastic/PVC/MDF/Steel |
Type | PCD/ MCD/ ND/ CVD/ CBN |
Features | No burs, high precision, good surface effects and high cutting efficiency and long work time |
Advantages | Factory direct sales, short delivery time; non-standard customization, quality assurance; attentive service, customer first |
Brand | Joeben |
Welcome and congratulations!You found us a professional factory! | |
Size & Design | 1.We not only supply all kinds of high quality solid carbide turning tool ,but also different types of Drill Bits,Reamers,Tool Holders,Cutter Heads,Saw Blades and Milling cutter,There are diamond grinding wheel, diamond dressing tools and hardness head. |
2. We have 0.02mm-25mm different diameter and 38mm-150mm length Milling Cutters for your winner market.HRC45/55/60/65 ,1-6 flutes for you to choose. | |
3.OEM:Special Cutters Customized acceptable!Coated OEM also.We can produceaccording to your drawing,too.Or the hot deisgned recommend to you. | |
4. HS Code reference for you to control everything:8207709000. | |
5. Mixed size and types in one batch available. | |
6. For distributor,we can label your brands on cutters and plastic box. | |
Plating | 1. We accept Mix coated in the same model number, Also one batch with different coating and types. |
2. AlTiN,TiAlN,TiSiN,TiN,DLC,NANO for you to choose to win your competitors! | |
MOQ (Small Qty ) | 5-10-500-1000-5000-10000 pcs all are welcome. 5 pieces per order is MOQ. |
OEM One-Step Packing | We package all our goods carefully.We also accept your packing design OEM packing it for your control. |
Samples Service | 1. Some items free samples for you. |
2. Free samples but pay shipping cost. | |
3. Lowest shiping fee for you to choose. | |
4. Order to us,sample fee will be refund to you. | |
5. Become our VIP clients,free samples for you! | |
6.OEM samples are hot welcome. |
Q:Are you Manufacture?
A:Yes, we are manufacture. we produce our “JOEBEN “brand tools for gurantee the quality.
We also trading related tools for customers because we are in these
field over 10 years, we are very familiar Chinese market tools. we
usually help our customer choose the best suitable related tools
for them.
Q: What is your delivery time?
A: Most of models are ex-stock, if out of stock,there usually need
about 3-5 days or 7-10 days.
Q: Can you produce non-standard tools?
A: Yes, we can produce non-standard tools as per your drawing.
We also can design tools for you as per your usage requirement
Q:What is your advantages?
A: We are factory who produce our own brand “JOEBEN” tools, we must gurantee our brand quality. Also, we have factory
price and fast delivery.
Our advantage:
ATTACTION: