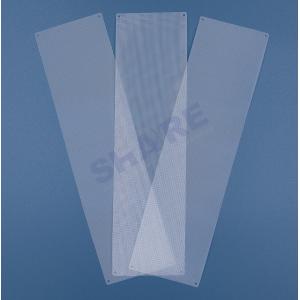

Add to Cart
SHARE has been customizing mesh components to fit our customers'
needs and applications for decades. We are able to convert filter
mesh fabrics into various specific pieces and shapes such as discs,
tubes, ribbons, shapes, cut-to-size sections. These are just a few
examples that SHARE processes with laser technology.
To ensure precision, speed and the ultimate product quality, SHARE
has made significant investments in its state-of-the-art laser
cutting operations.
At SHARE, precise filter fabric shapes are created using CAD
software and transmitted to high-speed, in house developed custom
laser cutting machines. As a result, you can rely on high-speed,
outstanding cutting, sealed edges, and the consistent quality
required by SHARE's world - class mesh filters - every time.
The main advantages of SHARE laser cutting of mesh filter pieces
and shapes:
1. High precision and repeatability
In house developed laser machines with built-in CAD softwares
ensure the cut pieces are precise and consistent.
2. Clean, burr free, non fraying cut edges
Woven fabrics can easily fray after cutting, but the heat generated
by the laser creates a small weld at the cutting edge. This weld
avoids fraying of the yarn.
3. No clamping of filter mesh
Laser cutting is a non-contact cutting technology, so the material
doesn't need to be fixed or clamped. There is no damage and
contamination to the material and thus increased production speed
as roll changes are faster.
4. Extreme high cutting speed
High speed laser machines combined with SHARE custom designed
roll-off mechanism to process filter material from rolls instead of
sheets. This results in significant faster production times with
monthly output at least 10, 000,000 pcs for small filtration discs.
Therefore, we ensure prompt delivery for standard orders.
Specifications
Item name | Laser cut burr-free polyester screen mesh filter pieces |
Manufacturer | Taizhou Share Filters Co. Ltd. |
Brand | SHARE FILTERS |
Material | 100% polyester monofilament yarn, other materials such as PA PE PP are available. |
Color | White or other colors |
Fabrication shape | Round, square, rectangular, trapezoidal, circular, irregualr, etc. It can be customized according to your request or drawings |
Mesh opening | 10-4000 microns for your option. |
Product process | Laser cut |
Sample | Available |
Features | Almost unlimited range of shapes Suited for healthcare applications Traceability Non-fraying sealed edges |
Certificate | ISO19001 SGS ROHS REACH |
Application | Liquid filtration, medical filtration, and semi finished fabricated mesh filters are particularly suitable for use in injection molding processes |
Product Gallery
Customers have different requirements for filtration & separation, and relying only on ultrasonics cutting technology is not sufficient to meet the challenges of today's demanding filtration market. Therefore, after years of developments, SHARE has developed expertise in almost all processing technologies, including cold cut&stamping, heat slitting, laser cutting, ultrasonics cutting, sewing, pleating, and injection molding etc.
Filter piece and shapes are essential for insert molding. We are happy to advise the best fabrication technology to customers
application and requirement.
Here are some examples of our fabricated nyllon(polyamide) mesh
filters:
Laser&ultrasonics cut polyester single or multiple layer irregular shapes
Laser cut and ultrasonics cut polyester tubes, ready for insert molding
Polyester strip ring, cut by laser and then welded by ultrasonics
Polyester cylindrical tube, mesh cut by laser and over-lapped welded to tube by ultrasonics
Polyester continuous tube
Polyester corner/edge welded tube cut
Polyester liquid filter bag
Polyester welded bag for medical filtration
Injection molding polyester mesh filters
We have created thousands of filtration solutions to help customers achieve the best filtration configuration and
solution for various applications, including appliance,
electronics, medical and healthcare, automotive, food and beverage,
mining, architecture, aerospace etc.
Please feel free to contact us for any filtration inquiry, and our
application specialists will be glad to provide our best filtration
solution for you.
Product Procedure
At Share, from yarn to product, every phase of production is
carefully monitored, employing frequent in-house testing and
rigorous inspection to ensure consistent quality at every step of
production. Mesh thickness, open area, mesh count and air
permeability are all subject to strict controls which result in
high quality final products.
Each batch of our filter meshes undergoes a meticulous process
involving at least twelve distinct steps, ensuring the ultimate
production of high-quality filtering products. The steps of SHARE
filter mesh production procedure are:
Yarn→Raw yarn inspection→Warping arranging→Drawing in heddle→Drawing in reed→Weaving→Initial survey→Washing→Heat setting treatment→Physical properties inspection→Products inspection→Product→Fabricated filter and screens if needed→Molded plastic filters if needed
Based on customer drawings or requirements, SHARE filter mesh can be further processed into various types of cut-to-size filter stamped discs, pieces, shapes, ribbons, tubes, bags, injection molded filter etc.
What SHARE can do for you?
Whether you want to improve the quality or reduce the cost of your
existing filter component, plan a new filtration application, or
need assistance with specifications and design validation, SHARE is
here for you. Our specialist problem solving skills are ready to
address any challenges you encounter.
By vertical integration of our global supply chain and expertise,
our extensive manufacturing and production facilities, our
experiences of filtration team, as well as our materials
management, we take end-to-end control of all the steps in the
manufacturing process, including weaving, fabrication, molding. Our
ability to efficiently manufacture products not only ensures
repeatable product quality, but also maintains a steady supply
chain, reduces production costs and shortens lead times for our
customers.
We aim to offer the most reliable and cost effective filter
solutions for all filtration applications. SHARE application speciallists with decades of experiences will
help you select the best filter solution for your application.
Contact SHARE today for additional information and how we can help
you with your specific filtration requirements.
Packaging & Shipping
For mesh rolls:
1. Rolled on the paper core, 30-70m/roll, packed into PE bags, the product label is attached on the edge of each roll
2. 2-8 rolls per standard export carton
3. Put into PP woven bag to prevent damage during transportation
4. Package belt strengthen
For fabricated & molded filters:
1. Packed into sealed PE bags, 10pcs to 500pcs/bag according to the
actual size, double bagged and the product label is attached in the
inner bag
2. Put into bigger PE bag and then standard export carton
3. Wrapped the outer carton with PE stretch film to prevent damage
during transportation
4. Package belt strengthen if pallets are available
The label contains the following standard information:
item name, manufacturer, material, dimensions, manufacturing date,
order number, batch number etc.
Port to Port | Door to Door | |
Express(DHL,UPS,FEDEX, EMS) | 1 - 5 days | |
Air Freight | 1 - 5 days | 4 - 10 days |
Sea Freight(FCL) | 15 - 30 days | 20 - 35 days |
Sea Freight(LCL) | 15 - 30 days | 22 - 37 days |
FAQ
1. Where is your factory located? How can I visit there?
We are in Taizhou city, Zhejiang province China. By train, we are
one hour away from Hangzhou and two hours away from Shanghai.
2. Can I get free samples and how long can you deliver them?
We are pleased to provide you with free samples for your evaluation, which will be sent to you within 2 days. Please feel free to reach out to us for samples.
3. How long does a quotation take?
In most cases, we respond within 2 days. If something in RFQ need be confirmed, we will promptly
notify you soon.
4. How quickly can I get my order finished?
The production lead time is dependent on the quantity. Typically,
it takes 5 to 15 working days for us to complete mass production once you have
placed the order.
5. What about your quality control?
By visual inspection, optical or pressure sensitive equipment and
automated 3D image-inspection equipment, our production operators
conduct self-inspections at every stage of the process.
Additionally, we have spot inspections and final inspections
carried out by our Quality Control (QC) team.
6. What's your largest advantage?
One of our core competencies is our excellent converting
capabilities from yarn over weaving to converted items with
professional technical team and quality guarantee and management
for more than 30 years.
7. What kind of payment terms do you accept?
T/T and LC and more.