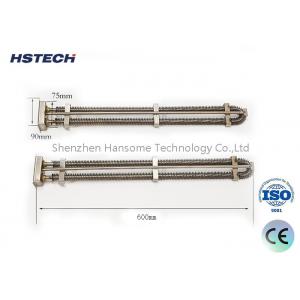

Add to Cart
JT Reflow Soldering / Wave Soldering Heating Wire High-Efficiency Heating Tube
Introduce
Heating wire is the most common type of heating element. Its function is to generate heat after being energized and convert electrical energy into thermal energy.
Reflow soldering is a group or point-by-point soldering process in
which an appropriate amount and form of solder is placed in the PCB
soldering area in advance, and then the surface mount components
are placed, using an external heat source to reflow the solder to
meet the soldering requirements.The heat required during the
working process is provided by a large number of heating wires
installed in the reflow soldering machine. Therefore, the heating
wire is an important part of the reflow soldering machine.
Feature
Compact size | Heating wires have a smaller volume compared to traditional heating elements, making them suitable for designing electronic devices and circuit boards with limited space |
Lightweight design | As heating wires are usually made of lightweight materials, they do not increase the load on the equipment and are suitable for scenarios that require lightweight design. |
Rapid heating | Due to its small size and high efficiency in energy conversion, the heating wire can quickly achieve heating, improving the response speed and efficiency of the equipment. |
Low power consumption | Due to the efficient energy conversion of the heating wire, it can achieve the required heating effect at a lower power, which helps to save energy and extend battery life. |
High reliability | The heating wire is fixed on the PCB through surface welding technology, and the connection is firm and reliable, not easily affected by vibration and impact, improving the stability and durability of the equipment |
Size selection
Detail display
Product Display
For the treatment of heating wires, the following steps are usually included:
1.Select appropriate heating wire specifications: Based on specific
application requirements and design requirements, select SMT
heating wires of appropriate specifications, including size,
resistance value, power, working voltage and other parameters.
2.PCB design and layout: In the PCB design stage, it is necessary
to reasonably layout the position of SMT heating wires and ensure
coordination with the layout of other components to ensure the
normal operation and stability of the circuit.
3.Welding process: Use surface mount technology (SMT) to solder the
heating wire onto the surface of the PCB. This usually involves
precise control of welding temperature, time, and pressure to
ensure welding quality and stability.
4.Quality inspection: After welding is completed, the welding
quality is inspected and tested. This includes visual inspection,
welding connectivity testing, as well as resistance and power
testing.
5.Assembly and packaging: Assemble the soldered PCB into the device
and package it to ensure the safety and reliability of the heating
wire and other components.
6.Testing and debugging: Test and debug the entire circuit to
ensure that the SMT heating wire can work properly and meet design
requirements and performance indicators.
7.Application and maintenance: After the equipment is put into use,
regularly inspect and maintain the SMT heating wire to ensure its
normal operation and long-term stability.
By following the above processing steps, the reliability and
performance of SMT heating wires in electronic devices can be
ensured, thus providing an effective heating solution.