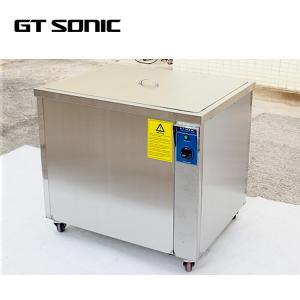

Add to Cart
Ultrasonic vibration cleaning machine Features:
1. Whole machine is made of SUS304 stainless steel, 2mm thickness
tank for acid-proof, anti-corrosive.
2. Industrial grade Ultrasonic transducer, moisture-proofed PCB.
3. Advanced generator, sweep frequency, high quality, better
effect.
4. Ultrasonic power can be adjusted from 0-100%.
5. Temperature can be set from 30-110°C.
6. Industrial grade for 24 hours of continuous working.
7. Ultrasonic frequency: 28kHz or 40kHz.
8. Fully portable, 36L and above volume machines with wheels,
locking wheels for stability.
9. With free lid and stainless steel SUS304 basket.
10. Customized according to customer’s request.
Specification
Model | Unit size | Volume | Ultrasonic Power | Ultrasonic Frequency | Heating power | Heating temperature |
(L×W×H)mm | (L) | (W) | (kHz) | (W) | (℃) | |
VGT-1012S | 530×430×600 | 40 | 720 | 28/40 | 2000 | 30-110 |
VGT-1018S | 630×480×650 | 65 | 1080 | 28/40 | 3000 | 30-110 |
VGT-1024S | 730×530×700 | 96 | 1440 | 28/40 | 4000 | 30-110 |
VGT-1030S | 790×590×700 | 117 | 1800 | 28/40 | 4000 | 30-110 |
VGT-1036S | 840×640×750 | 157 | 2160 | 28/40 | 5000 | 30-110 |
VGT-1042S | 890×690×800 | 206 | 2520 | 28/40 | 6000 | 30-110 |
Application:
Electronics:
An Ultrasonic vibration cleaning machine gets a safe, unwavering
cleaning for even the most delicate of components. GTSONIC baths
completely remove flux and contaminants from such precision parts
as PC boards, SMDs, quartz crystals, capacitors, and many others.
Auto parts:
Ultrasonic technology is changing today’s parts cleaning industry
by making precision cleaning safer, faster, less expensive, and
more effective. Ultrasonic cleaners offer results far beyond
traditional cleaning methods, for everything from carburetors to
medical instruments.
Industrial:
The solid, sturdy structure and high-tech design make our
Ultrasonic vibration cleaning machine the perfect business. We
manufacture standard systems from one to 206 liters, designed to
handle Ultrasonic cleaning parts in a variety of shapes and sizes.
What is Ultrasonic?
Ultrasonic refers to sound waves that have a frequency higher than
the upper limit of human hearing, which is generally considered to
be around 20 kilohertz (kHz). In other words, ultrasonic waves are
sound waves that vibrate at a frequency greater than 20,000
vibrations per second.
Ultrasonic waves are produced using a device called an ultrasonic transducer, which converts electrical energy into high-frequency mechanical vibrations. These vibrations are then transmitted through a medium, such as air or water, and can be used for a variety of applications.
One of the most common applications of ultrasonic waves is in ultrasonic cleaning, where high-frequency sound waves are used to create microscopic bubbles in a cleaning solution. These bubbles then collapse upon contact with the surface being cleaned, generating a powerful scrubbing effect that can remove even the most stubborn stains and debris.
Ultrasonic waves also have a range of other applications, such as in medical imaging, non-destructive testing, and industrial processing. In medical imaging, ultrasonic waves are used to create images of internal organs and tissues, while in non-destructive testing, they are used to detect flaws in materials and structures. In industrial processing, ultrasonic waves can be used for welding, cutting, and cleaning, among other applications.
What is De-gassing?
Degassing refers to the process of removing dissolved gases from
liquids or solids. When liquids or solids are exposed to
atmospheric pressure or changes in temperature, gases such as
oxygen, nitrogen, and carbon dioxide can become dissolved in the
material. Over time, these dissolved gases can create problems such
as corrosion, foaming, and reduced performance.
The degassing process involves exposing the material to a reduced-pressure environment, such as a vacuum chamber or a degassing unit. The reduced pressure causes the dissolved gases to come out of the solution and escape from the material, usually in the form of bubbles. The bubbles are then removed from the material, either by vacuuming them away or allowing them to rise to the surface and escape.
There are many applications for degassing, including in the production of electronic components, where the presence of dissolved gases can interfere with the performance of sensitive components such as microchips and circuit boards. Degassing is also used in the production of pharmaceuticals, where the presence of dissolved gases can affect the quality and purity of the final product. Additionally, degassing is used in the production of food and beverages, where dissolved gases can affect the taste, appearance, and texture of the final product.
Product Details: