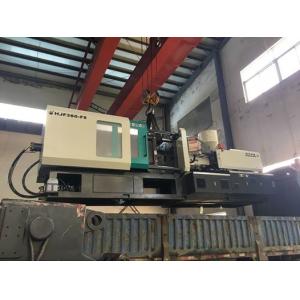

Add to Cart
Just as with overall product design, mold design is another opportunity to prevent defects during the injection molding process. We have previously written blogs on the Top 10 Injection Molding Defects and Avoiding Mistakes in Injection Molding, but here are some examples of how poor mold design can be a costly mistake:
Not designing the proper draft: This refers to the angle at which the finished product is ejected from the mold. An insufficient draft can lead to ejection problems, costing significant time and money.
Improperly placed or sized gates: Gates are the openings in a mold through which thermoset or thermoplastic material is injected. Each will leave a vestige (scar), which can create aesthetic or functional problems if not properly placed.
The number of parts (cycles) required, as well as the material they will be made of will help drive decision-making as to how and with what materials to create the mold.
When a product has been properly designed, approved, and die cast, it’s time to start the actual manufacturing! Here are the basics of the injection molding process…
Thermoset or thermoplastic material in granular form is fed through a hopper into a heating barrel. (Learn more about the differences between plastics in our PLASTICS course.) The plastic is heated to a predetermined temperature and driven by a large screw through the gate(s) and into the mold. Once the mold is filled, the screw will remain in place to apply appropriate pressure for the duration of a predetermined cooling time. Upon reaching this point, the screw is withdrawn, the mold opened, and the part ejected. Gates will either shear off automatically or be manually removed. This cycle will repeat over and over, and can be used to create hundreds of thousands of parts in a relatively short amount of time.
SPECIFICATION | HJF-140 | |||
A | B | C | ||
Screw Diameter | Mm | 38 | 42 | 45 |
Screw L/D Ration | L/D | 22.1 | 21.6 | 19.5 |
Shot Size(Theoretical) | cm3 | 193 | 227 | 278 |
Injection Weight(PS) | g | 176 | 206 | 252 |
Injection Rate | g/s | 94 | 105 | 135 |
Injection Pressure | MPa | 205 | 159 | 140 |
Screw Speed | rpm | 0~220 | ||
Clamp tonnage | KN | 1400 | ||
Opening stroke | mm | 380 | ||
Space Between Tie Bars | mm | 420*420 | ||
Max.Mold Height | mm | 450 | ||
Min.Mold Height | mm | 170 | ||
Ejector Stroke | mm | 120 | ||
Ejector Tonnage | KN | 33 | ||
Max.Pump Pressure | MPa | 16 | ||
Pump Motor Power | KW | 13 | ||
Heater power | KW | 7.2 | ||
Machine Dimension(L*W*H) | M | 4.5*1.2*1.7 | ||
Machine weight | T | 4.2 | ||
Oil Tank Capacity | L | 230 |
Servo Machines Features
1. High energy savings
Under normal operating conditions, compared with conventional
hydraulic injection molding machines, energy savings of 20-80%
can be achieved.
2. Molding stability
Compared with conventional injection molding machines repeatability is greatly improved due to servo motor closed-loop control.
3. Quick response
Featuring a dynamic servo motor with a response time of only 0.05sec
4. Quiet operation
The machine runs at much lower noise levels, particularly in low speed applications.
5. Reliable holding pressure
Compared with traditional hydraulic machine the holding pressure is more stable and does not have limitation.
6. Better oil temperature stabitily
The servo system only delivers hydraulic oil as it is needed for the various functions. This prevents unnecessary generation of heat and substantially reduces oil cooling requirements.
Servo energy-saving system
Using the servo motor oil esectriciyt composite sturcture, high response, low noile and excellent
electricity -saving performance.
■ Computer Controller PLC
Professional injection moulding machine controller with software and hardware of industrial standard is convenient to expansion and revision of performance.
Adopting double CPU control makes high speed.
Mainly adopting PID control, the control accuracy reaches±1°.
Has the function of network management, improving efficency.
■ The Mould Adjusting Units
The automatic mold adjusting device driven by hydraulic motor adopts gear coupling drive, features steadiness, high-efficiency and saving mold loading time.