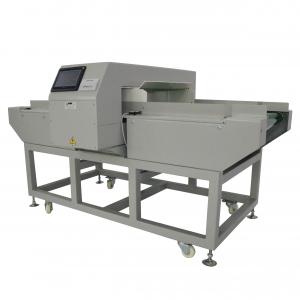

Add to Cart
Factory capability & capacity assessment needle detector for
garment / garment needle detector / garment metal detector
About Shanan.pdf
Company introduce:
SHANAN is a manufacturing company specialized in the design,
engineering and production of Metal Detectors .check weigher
.needle detector and Electromagnetic Inspection Devices.we offering
solution for food industry ,Pharmaceutical industry , Textile
garment industry ,Rubber industry .Tory industry where the factory
need help to control their quality for find broken needles and
metals .
Under our solution and machine support our valued customer can
accreditation with the FDA ,ISF ,HACCP even FCCA request and
requirement .
Function :
General Specifications
● Equipped withSHANAN microcomputer chips from USA for digital
signal management, it can analyze the different channel signals and
improved the detection reliability.
●Special inducing design in the detection field, the sensitivity
and anti-disturbance ability are greatly improved, and it is not
disturbed by the environment.
● Unique inducting design of balanced magnetic field to meet the
needs of different clients, especially for the detection of garment
accessory.
● With digital display in Chinese, touching screen of films. It is
convenient for operation and management.
● The perfect combination of powerful functions and simple
operation is also a friendly philosophy of design.
● Equipped with the intellectual location displaying system, which
can indicate the location of the needle.
● The intellectual counter system can caulate the qualified and
unqualified objects amount.
● Equipped with safe lock only, which can lock the sensitivity, so
that it is convenient for management.
● Digital sensitivity regulation, the induction strength can show
the disturbance and Iron content.
● Equipped with light control automatic alarm and automatic power
off function.
Metal Detector Calibration Checklist:
Switch on the machine and set the sensitivity level to less than
1.2mm sphere.
Position the test card directly onto the conveyor belt at position
A1.
Let the card pass through the search head.
The metal detector is being activated and the alarm is sound.
Repeat the above steps 1-3 with the test card in positions A2 and
A3.
Again the detector is being activated and the alarm is sound.
The test card is putting through on its own, we are not put it on a
paper or put it through with a garment.
Repeat steps 1-3 with the test card positioned in the middle of a
stand (7-8cm high) or on top of a stand that is around 3-4cm high
(depending on the height of the gap between conveyor belt and top
of machine) at positions A4, A5, A6.Again the metal detector is
being activated and the alarm is in sound. The stand are being a
non-detectable block made of plastic material.
Repeat steps 1-3 with the test card on the top of a stand (7-8cm
high or as high as the gap allows for) at positions A7, A8, A9 and
again the metal detector calibration procedure are being activated
and the alarm are in sound.
Records are being kept of all of these checks by using the
prescribe form.
In case the machine fails to pass the calibration test, it is
immediately being turned off and re-calibrated by an authorised
technician. All goods checked after the last calibration is being
re-checked once normal operations of the detector have been
re-established.
Machines are being calibrated at least every 6 months by the
manufacturer.
Calibration certificates are being obtained and being kept for
auditing purposes.
If for any reason the detector are being relocated, it is being
re-calibrated by the supplier’s authorised technical service.
Regular maintenance (at least annually) of the detector is being
carried out by the supplier’s authorised technical service based on
the periods set up by them. Records for maintenance and any
re-calibration made by the supplier are being kept, in case these
need to be provided during any audits.
Metal detection:
When performing the metal detection it is being ensured that
products are placed on the moving conveyor belt one by one with
sufficient space in between products, so that there is no overlap.
If goods are being shipped e.g. on hangers that are ferrous and
cannot be passed through the metal detector, the goods are being
taken off the hanger, passed through the metal detector and then
re-hung. It is permitted for the hangers to be moved through the
metal via a door. This process are controlling by the authorised
person and only the correct amount of hangers per order are to be
held at any one time, no spare hangers to be stored.
As a general guideline though garments be metal detected as last as
possible in the production process and any ferrous metal items are
being attached in the metal free zone, such as security tags,
hangers etc.
The metal free zone are not being used for general storage and are
being tidy. Once product is boxed or hung is to be taken to
dispatch.
Handheld metal detector also used for this
In case of stone washing the garments are being metal checked prior
to washing as the pumice dust contains small metal particles that
have an adverse effect to metal detection.
Any garments or part of a garment that are being outsourced for the
application of a print, embroidery or any other process are being
metal detected upon receipt back into the factory, prior to
continuing production. This is to ensure that no whole or broken
needle pieces, staples, other stray metals or sharp objects are in
the returned pieces.
The factory are making sure that procedures are in place to ensure
that all garments including repaired and re-inspected do not go to
packing without being checked by the detector.
Clear separation and identification of the garments that are
waiting to be checked and that are being checked to be strictly
made.
Records are being kept for all garments that are passing through
the metal detector and are being completed as product passes
through the machine to verify compliance with this requirement.
If the alarm sounds, all garments on the halted conveyor belt are
being put into a sealed bag, segregated and locked in a secure
rejection box, to be located near the metal detector.
The rejection bin are being taken to a clearly marked area and
thoroughly checked for contamination by the assigned person.
If the metal parts are found and the garment passes through the
conveyor industrial metal detectors successfully, the garment can
be returned to the bulk.
If the metal part cannot be found, the contaminated product are
being put into a polybag with details clearly marked on it and then
placed inside the rejection bin (s. photo) locked away from the
factory floor and THE GARMENT ARE BEING DESTROYED after authorised
sign off by the factory manager.
Parameter :
MODEL | SHANAN NEEDLE DETECTOR | |||||
Detection method | Magnetic induction.digital process double sensor | |||||
Detection ability | ≥FeΦ0.8 | ≥FeΦ0.8 | ≥FeΦ1.0 | ≥FeΦ1.2 | ≥FeΦ1.5 | ≥FeΦ2.0 |
Detection Height | 100mm | 120mm | 150mm | 200mm | 250mm | 300mm |
Detection width | Net width 600mm-non-standard sizes(custom) | |||||
Detection adjustment | Touch screen adjust the level 1-12 | |||||
Alarm method | Sound/light alarm and return, then restarts again | |||||
Power supply | Ac220V 50-60Hz | |||||
Pated output | 140W | |||||
Machine Size | L1820mm×W1050mm×H900mm | |||||
Weight | 280KG |
Use Range :
Garment .Textile.underwear .towel. Sanitary and so on industry .