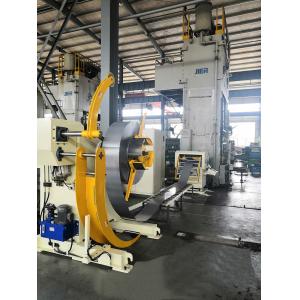

Add to Cart
The feeder is an auxiliary mechanical device used with a punching
machine. Its function is to automatically transport the metal or
non-metal plate into the die position of the punching machine, and
the material of the punching machine gradually presses the material
into the cavity of the die.
At present, the most used in the stamping industry is the roller
feeder, which is powered by the output shaft of the punching
machine through the eccentric disk, the cross joint, the tie rod,
the rocker arm and the transmission shaft. The final power source
of the roller feeder is the punch output shaft. .
Therefore, the synchronization performance of the feeder and the
punching operation is accurately guaranteed, and the stamping owner
is also well understood, but this also causes a problem.
That is, once the feeding step required for the stamping process
changes, it takes a long time to adjust the test machine time. In
actual use, the labor intensity is high, the professional
requirements are high, and the time is long.
As a new type of CNC feeding equipment, NC feeder is one of the purpose of its purpose is to simplify the debugging,
test procedure and time of traditional feeders and reduce labor
intensity.
Its step setting is very simple, just need to simply input on the
NC feeding electrical control box touch screen.
In fact, the principle of synchronizing the NC feeder with the
punch is not complicated. Simply speaking, the PLC of the NC feeder
receives the angular angle signal transmitted by the punch crank
encoder.
Through the operation, the feeding and loosening actions are
realized at the specified timing, thereby achieving the purpose of
running synchronously with the punching machine.
To ensure the accuracy of each feeding and the reliability of the
stamping, the actual installation method for this effect is also
very simple, just need to take out two sets of cam signals from the
punching machine (one set is the feeding signal and one set is the
relaxation signal).
Then connect it to the PLC in the NC feeding electrical control
box, and the PLC can precisely control the feeding action of the
servo system to achieve perfect cooperation with the punching
machine.
Specification:
Model | MAC2-400 | MAC2-500 | MAC2-600 | MAC2-800 | ||
Stock Width(mm) | 50-400 | 50-500 | 50-600 | 50-800 | ||
Stock Thickness(mm) | 0.3~3.2 | 0.3-3.2 | 0.3-3.2 | -3.2 | ||
Max.Coil Weight(kg) | 3000 | 3000 | 3000 | 5000 | 5000 | 7000 |
Max.Coil O.D.(mm) | 1200 | 1200 | 1200 | |||
Coil I.D.(mm) | 8 | 8 | 508 | 508 | ||
Feed Length(mm) | ~500* | ~500* | ~500* | ~500* | ||
Max. Line Speed(m/min) | 16-24 | 16-24 | 16-24 | 16-24 | ||
Work Roll Number(pieces) | upper 6 lower 5 | upper 6 lower 5 | upper 6 lower 5 | upper 6 lower 5 | ||
Feed Roll Number(set) | 1 | 1 | 1 | 1 | ||
Main Motor(kw) | AC2.9 | AC2.9 | AC4.4 | AC4.4 | ||
Mandrel Expansion | hydraulic | hydraulic | hydraulic | hydraulic | ||
Reel Motor(kw) | 1.5 | 1.5 | 1.5 | 2.2 | 2.2 | 3.7 |
Power(V) | 3 Phase 220V/380V/50HZ | |||||
Operating Air(Mpa) | 0.49 | 0.49 | 0.49 | 0.49 |
Straigtening performance:
tock Thicknees (mm) | Stock Width (mm) | |||
0.3 | 400 | 500 | 600 | 800 |
0.4 | ||||
0.6 | ||||
0.8 | ||||
1.0 | ||||
1.2 | ||||
1.4 | ||||
1.6 | 470 | 470 | ||
1.8 | 400 | 400 | ||
2.0 | 360 | 360 | ||
2.3 | 300 | 300 | 300 | 300 |
2.5 | 230 | 230 | 230 | 230 |
2.8 | 150 | 150 | 150 | 150 |
3.2 | 110 | 110 | 110 | 110 |
*1:(Pneumatic):Option in case of pneumatic mandrel expansion is
provi