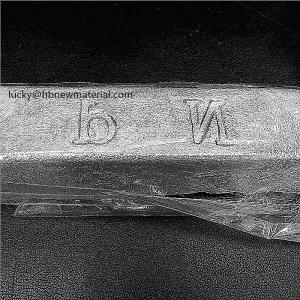

Add to Cart
MgNd30 Magnesium Neodymium Alloy Ingot For The Metal Industry Uses Master Alloys To Adjust The Properties Of Its Product
Master Alloy
One of the important functions of interalloys is that when smelting
alloys with very different melting points, the pre-prepared master
alloy has a lower melting point than pure elements, ensuring that
the added elements are melted. In Mg-Li alloys, alloying elements
with lower solid solubility and higher density (such as Zr, Mn, Ce,
etc.) are usually added in the form of Mg-X master alloys, or in
the form of compounds (usually salts). Through its reaction with
Mg-Li alloy liquid to generate alloying elements, this method can
effectively reduce the segregation and precipitation of elements.
The main purpose of adding the master alloy is to melt the elements
with a large difference in melting point (the composition is near
the eutectic point to lower the melting point), and make it lower
than the smelting temperature of the main element (smelting
generally takes the main element as a reference), This is conducive
to the progress of the smelting process. For example, Al-Si, Al-Cu,
etc. in Al alloys, generally the melting point of non-main elements
of the master alloy is higher than the melting point of the main
elements.
Master alloy, which is mainly used to modify the alloy. Its
organizational state is more critical and can affect the final
structure of the modified alloy. There are also many unstable
elements or elements that are difficult to alloy in the master
alloy. At the same time, master alloys, especially master alloys
used for modification, have a time limit (validity period) in use.
MgNd,MgY,MgZr,MgLi,MgSc,Mg with rare earth master alloy
Melt purification
Rare earth elements have the functions of removing hydrogen,
removing oxygen, removing sulfur, removing iron, and removing
inclusions in the magnesium alloy melt, achieving the effect of
degassing, refining and purifying the melt.
Melt protection
Magnesium alloys are extremely easy to oxidize and burn during the
smelting process. Industrial production of magnesium alloys
generally uses flux covering or gas shielding, but there are many
disadvantages. If the ignition temperature of the magnesium alloy
melt itself can be increased, it is possible to achieve magnesium
alloys. Direct smelting in the atmosphere is of great significance
to the further promotion and application of magnesium alloys. Rare
earth is a surface active element of magnesium alloy melt, which
can form a dense composite oxide film on the surface of the melt,
effectively preventing the melt from contacting the atmosphere, and
greatly increasing the ignition temperature of the magnesium alloy
melt.
Fine grain strengthening
The enrichment of rare earth elements at the front of the
solid-liquid interface causes the composition to be supercooled,
and a new nucleation zone is formed in the supercooling zone to
form fine equiaxed crystals. In addition, the enrichment of rare
earth makes it play a role in hindering the growth of α-Mg grains.
Further promote the refinement of the crystal grains. According to
the Hall2Petch formula, the strength of the alloy increases with
the refinement of the grain size, and compared with body-centered
cubic and face-centered cubic crystals, the grain size has a
greater impact on the strength of hexagonal close-packed metals, so
the grains of magnesium alloys are refined The resulting
strengthening effect is extremely significant.
Solid solution strengthening
Most of the rare earth elements have high solid solubility in
magnesium. When the rare earth elements are dissolved in the
magnesium matrix, the difference between the atomic radius and
elastic modulus of the rare earth elements and magnesium will cause
lattice distortion in the magnesium matrix. The resulting stress
will hinder the movement of the dislocations, thereby strengthening
the magnesium matrix. The effect of solid solution strengthening of
rare earth elements is mainly to slow down the diffusion rate of
atoms and hinder the movement of dislocations, thereby
strengthening the matrix and improving the strength and high
temperature creep properties of the alloy.
Dispersion enhancement
Rare earth and magnesium or other alloying elements form stable
intermetallic compounds during the alloy solidification process.
These rare earth-containing intermetallic compounds generally have
the characteristics of high melting point and high thermal
stability. Internally, it can pin the grain boundary at high
temperature, inhibit the slip of the grain boundary, at the same
time hinder the movement of dislocations, and strengthen the alloy
matrix.
Aging precipitation strengthening
The higher solid solubility of rare earth elements in magnesium
decreases with the decrease of temperature. When the single-phase
solid solution at high temperature is rapidly cooled, an unstable
supersaturated solid solution is formed, and after a long period of
aging, a small and dispersed solid solution is formed. The
precipitation phase of precipitation. The interaction between
precipitated phases and dislocations increases the strength of the
alloy.