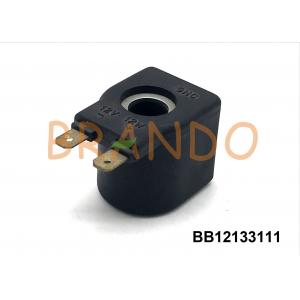

Add to Cart
Atiker/Tomasetto Type LPG/CNG Reducer Solenoid Coils MVAT3752/MVAT3578 BC.170/176/171 DC12V
The working principle of the CNG vehicle natural gas pressure reducing valve with Atiker/Tomasetto Type LPG/CNG Reducer Solenoid Coil is that there are three decompression chambers to achieve three-stage decompression. The first stage reduces the high pressure to the low pressure; the second stage adjusts the distribution; the third stage of the cng pressure reducer is controlled release.
The high-pressure compressed natural gas comes out of the gas
storage cylinder, is filtered by the natural gas filter, and enters
the high-pressure pressure reducer through the high-pressure
solenoid valve. The opening and closing of the high-pressure
solenoid valve is controlled by the ECM, and the high-pressure
pressure reducer functions as a high-pressure compressed natural
gas. (Working pressure 200bar-30bar) The pressure is adjusted to
7bar-9bar by heating under reduced pressure. High-pressure natural
gas needs to absorb a large amount of heat due to pressure
expansion during decompression. To prevent the pressure reducer
from freezing, the engine coolant is taken out from the engine to
the pressure reducer to heat the gas.
Technical parameter of Atiker/Tomasetto/Lovato/Tesmon Type Reducer Solenoid Coils:
Model number | BB12133111 |
Normal voltage | DC12V (Other can be customized) |
Normal power | DC:12W |
Insulation class | H |
Connection type | 6.3x0.8mm Faston |
Application | Atiker/Tomasetto/Lovato/Tesmon Type Reducer |
Weight | 84 g |
Hole size | 12 mm |
Height | 33.1 mm |
Width | 30 mm |
Main dimension of MVAT3752/MVAT3578 Tomasetto type solenoid valve coils:
Applicaiton of BC.170/176/171 ATIKER Type Reducer Electromagnetic Coils:
Production of DC12V 6.3x0.8mm LPG/CNG Faston Type Electric Magnetic Coils:
Function of LPG/CNG reducer with MVAT3752/MVAT3578 BC.170/176/171 solenoid coils:
According to the physicochemical properties of gas, the volumetric energy density of CNG and LPG is very low in the gaseous state. In order to improve the mileage of a gas vehicle inflated, the natural gas for vehicles is generally compressed to 20 MPa and stored in a high-pressure gas cylinder, while the LPG is pressurized to about 1.6 MPa into a liquid state and stored in a cylinder. However, when the engine is working, the gas pressure is required to drop to 1~2.5KPa to enter the mixer to mix with the air and enter the cylinder. Therefore, a pressure reducer must be provided in the gas supply system. At the same time, the engine uses gas as well as fuel, and it needs to deliver fuel to the cylinder at a certain air-fuel ratio. The air-fuel ratio control of the gas supply system is also the same as that of the fuel supply system, and does not vary with the amount of fuel in the fuel tank. Since the pressure of CNG gas in the high-pressure gas cylinder changes continuously with the filling and use of the fuel, it is necessary to maintain a relatively stable air-fuel ratio control, and it is also required that the pressure reducing regulator should also ensure the gas entering the mixer regardless of the change in the pressure inside the bottle. The pressure is essentially constant to achieve a relatively stable gas to air mixing ratio control.
In CNG vehicles, the role of CNG pressure reducers is mainly to
reduce pressure and voltage regulation, so it is generally called a
pressure reducing regulator. The role of the pressure reducer on
the LPG vehicle is mainly to evaporate the liquid petroleum gas
into a gaseous state, as well as decompression and voltage
regulation, so it is generally called an evaporation damper. Since
a large amount of heat is absorbed during the decompression
process, a water jacket for introducing engine circulating water
into the pressure reducer is generally provided on the pressure
reducer, and the heat exchanger is heated by the heat of the engine
circulating cooling water.
Pressure reducing regulators are a key component of gas vehicles.
The pressure reducing regulator can be divided into split type and
combined type according to the assembly mode of the multi-stage
decompression chamber; according to the control mode, it can be
divided into high-pressure cut-off control type and medium-pressure
cut-off control type; according to the output to the carburetor
Pneumatic type can be divided into positive pressure intake and
negative pressure intake.
Welcome to your inquiry!