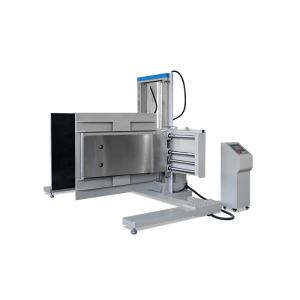

Add to Cart
ASTM D6055 Package Testing Equipment , PLC Control Package Clamp
Force Testing Machine
Specifications
ASTM D6055 PLC control package clamp force testing machine
1.Package clamp testing machine
2.Up to ASTM D6055
3.PLC control
Safety protection
Overload protection, overvoltage protection & limited position
protection device
Clamp Compression Testing Method of Large Products
1.Before placing the packaged product between platens, verify that
the clamp force using the clamp indicator. The indicator should be
placed between the axes of the platen articulation points
approximately 1/2 way up the platens.
2.Each time the product is clamped, the force should be applied for
a minimum of 15 seconds and not to exceed 1 minute.
3. Apply the clamp force on the sample with the platens resting on
the floor and the front edge of the platens flush with the front of
the package (see flush platen photo 4). If the package is too large
for the clamps to be flush to front edge (i.e., large refrigerator,
tractor etc.), clamp as close to the edge as possible.
4. Clamp the product a total of 10 times in the flush orientation.
5. Apply the clamp force on the packaged product with the platens
in a 6×6 inch(15.2x15.2cm) offset position(see fig 5 ). Both the
horizontal and vertical offset dimensions are measured at the front
bottom corner of the platen. If the package is too large for the
clamp to be positioned 6-inches from the front edge (i.e., large
refrigerator, tractor etc.), clamp as close to this position as
possible.
1)Exception number 1: for large products with an obvious, visible
external skid(see fig 6), offset clamp testing is not conducted if
the product does not extend beyond any part of the skid and there
is some form of handling graphic or note that indicates to clamp
only from the skid. If there is no graphic or not indicating this
or there is some overhang beyond the skid, then the entire clamp
test protocol is conducted.
2) Exception number 2: If the product height, when placed in its
normal shipping orientation, is ≤ 12 inches, the 6 x6 inch offset
testing is not conducted.
6. Clamp the product a total of 10 times with the clamp in the 6 x6
inch offset position.
7. Repeat step 5.2.5 except with a 2 x6 inch offset clamp position.
The 2 x6 inch offset is similar to the 6 x6 inch offset except the
platens are oriented such that they are 2-inches from the floor and
6-inches back from the package’s front edge. If the package is too
large for the clamps to be positioned 2-inches from the front edge
(i.e., large refrigerator, tractor etc.), clamp as close to this
position as possible.
8. Repeat flush and offset clamping on all other sides of the
product that are indicated in the handling graphics as acceptable
for clamp handling.
According to verdict standards, if there is one item failed the
test, then put forward the “Test Failure Handling Sheet
The Parameters
Design standard | ASTM D642, ASTM D6055, American SEARS enterprise standard |
Sample shape | parallelepiped transport package |
Maximum test weight | 500KG |
Clamping pressure | 400-3000Lb (adjustable) pressure can be applied on the corresponding surface according to the transportation diagram on the test sample |
Plywood size | H48in * D48in |
Clamping plate height adjustment | 0-1000mm |
Lifting speed | 50-300mm / min, set fixed speed |
Spreading plate width | 200-2000mm |
Dimensions | 2000 * 2800 * 2350mm |
Sensor accuracy | 1/100000 |
Measurement accuracy | 1% |
Clamping displacement accuracy | ± 0.5MM |
Power controller | Touch screen Chinese display maximum power value burst |
Splint requirements | Two gripping plates are 2000lb parallel and flat without deformation under working conditions, the vertical state between the splint and the floor, the thickness of the splint is ≥15mm, the splint can realize the action and cycle of clamping, opening, rising, and lowering cycle |
Automatic stop mode | set the upper and lower limits to stop |
Transmission mode | servo motor controls clamping force, and AC motor controls rise and fall |
Protection device | leakage protection, travel limit device |
Working voltage | AC 220V / 50HZ |
Clamp Compression Testing Method of Small Products
Before clamp testing, verify that the clamp for using the clamp
force indicator. The indicator should be placed between the axes of
the platen articulation points approximately 1/2 way up the
platens.
During clamp compression testing of small products, 4 samples will
be utilized as outlined below.
1. If, when oriented for clamp testing (based on the handling
graphics) the sides perpendicular to the platens of a single sample
≤ 24” (61cm), then the 4 sample should be placed in a”side by
side”oritentation as shown to the fig 1(with 2 samples on the
bottom and 2 on the top)
2. If, when oriented for clamp testing the sides perpendicular to
the platens of a single sample are >24” (61cm),, then the 4
samples should be placed in a top-bottom orientation as shown fig
2. If, when placed 4-high, any of the samples are completely above
the top of the platens, that sample can be removed from clamping in
this orientation only(fig 3 shows 3 MHC’s ready for clamp testing
with the 4th sample removed from testing in this orientation)
3 Each time the samples are clamped, the force should be applied
for a minimum of 15 seconds and not to exceed 1 minute.
4 .Apply the clamp force on the samples with the platens resting on
the floor and the samples flush with the front edge of the platens
(see fig2). If the samples are too large for the clamps to be flush
to front edge, clamp as close to the edge as possible.
5.Clamp the product a total of 10times with the clamps in the flush
orientation.
6. Apply the clamp force on the packaged product with the platens
in a 2×2 inch offset position(see fig 3). Both the horizontal and
vertical offset dimensions are measured at the front bottom corner
of the platen. If the package is too large for the clamps to be
positioned 2-inches from the front edge, clamp as close to this
position as possible.
7. Clamp the product a total of 10 times with the clamps in the
offset position.
8. Repeat the flush and 2x2 inch offset camping on all other sides
of the product that are identified in the handling graphics as
acceptable for clamp handling. Please note, depending on the box
geometry, you may use both the side-by-side and top-bottom
orientation during clamp testing.